News

1684857798000
How to plan a Coiled Tubing Drilling operation
Adam Miszewski, Global Operations Manager at AnTech Ltd explains how to plan a CTD operation. Above: Figure 1. AnTech's crew preparing their COLT BHA for drilling. Directional Coiled Tubing Drilling (CTD) has been used successfully in fields across the USA including: Alaska, Texas, California, Kansas, and Michigan amongst others (Figure 2). The established technique revitalizes mature oil and gas fields and, in particular, there has been high growth in deployment across the Middle East with a doubling of the CTD rig count over the last few years and further growth expected in the coming years. Why use Coiled Tubing Drilling The reasons for using CTD vary depending on the application. The main reasons are: thru-tubing or slimhole sidetracks, underbalanced drilling, high pressure wells which require specialist Managed Pressure Drilling/Underbalanced Drilling (MPD/UBD) and remote operations. The most commonly used BHA diameter for CTD is 3-1/8” with larger tools available with 5” OD and smaller tools available with 2-3/8” OD (Figure 3). The BHA sizes are limited to 5” or below due to the practical limits on the size of coiled tubing. The technique is most suited to smaller hole sizes such as 8-1/2” or below, with most wells drilled with a hole size less than 4-1/4”. Therefore, the benefits usually stem from re-entry drilling or shallow gas or oil wells. An alternative way to think about CTD is that it is a reservoir drilling technology so the closer to the reservoir the more advantageous CTD will be. Figure 2. Coiled Tubing Drilling operations undertaken in Pampa, Texas, USA. Drilling safely and efficiently Coiled tubing is designed for underbalanced operations and continuous circulation as standard. Therefore, mature fields with low pressure can be drilled underbalanced safely and efficiently with the reservoir rock protected from damage – critical when there is little pressure to drive production. Although underbalance can be achieved with a single-phase fluid in high pressure reservoirs, this is particularly relevant to fields requiring a two-phase drilling fluid, such as water and nitrogen, as a stable circulating regime can be maintained at all times. Also, some fields are not able to use EM telemetry and, therefore, wired CTD tools are the only option in two-phase systems. Drilling high-pressure wells Coiled tubing also has significant advantages for drilling high pressure wells either using managed pressure or underbalanced drilling techniques. This is due to continuous circulation and high-pressure control equipment as standard. The continuous circulation allows for better control of downhole pressure through adjustable pumping rates in addition to drilling fluid weight and choke pressure. Pressure control equipment of up to 15,000psi is also relatively standard. Drilling offshore Coiled tubing drilling is also advantageous in offshore projects in terms of the type of slot recovery, equipment footprint, and cost reduction. CTD operations can be carried out through tubing which removes a significant amount of the slot recovery operations. Due to the size of the equipment, CTD can fit on most platforms and does not require the use of a jack-up rig and thereby reduces the cost of the new wellbores and minimise the crew numbers required to do the work. This is in addition to the advantages of MPD on coiled tubing. Drilling in remote locations The smaller, more mobile coiled tubing equipment gives an advantage over conventional rigs in remote locations, for example, Northwestern Australia. This can be critical to the commercial success of small projects. However, a combined approach with a conventional rig can instead be the optimum solution. For example, utilizing a conventional drilling rig to drill the well down to the reservoir and then using the CTD package to drill the reservoir, ideally underbalanced, optimizes the benefit of each technology. In addition, it also means more wells can be drilled in a set period of time than with a single rig or for lower cost than mobilizing two drilling rigs. This is before the improvements to production are factored in from drilling underbalanced. When not to use CTD There are situations where CTD is not suitable. The largest hole size ever drilled directionally with CTD is 8-1/2” and currently the technology is unable to drill larger diameters. CTD has been used successfully to drill new wells from surface, however, this requires specialist, hybrid coiled tubing units, which can be difficult to source. When a hybrid unit is available, they are usually depth limited and, therefore, only suited to shallow wells. Consequently, operations requiring large hole sizes and casing running operations are unlikely to be suitable for CTD. Another limitation of CTD packages is in cementing. Due to the wireline inside the coil required to operate the BHA, any cementing operations become very time consuming, due to the resultant slack management, or the expense of needing a second standard coiled tubing string available for that operation. Figure 3. AnTech's 3-1/8” COLT BHA. Equipment requirements A coiled tubing drilling package requires the same fundamental equipment as a conventional drilling package:a “rig”, a fluids and solids control package, and a downhole drilling tools. All coiled tubing units can be used for CTD re-entry operations within the limits of their capacity. However, CTD requires coiled tubing with wireline inside, commonly referred to as e-coil. Consequently, a collector bulkhead and a slipring collector need to be installed to allow an electrical connection from outside the reel to the wireline inside the coil and to the BHA. The fluids and solids control equipment utilized will be heavily dependent on whether or not the well is going to be drilled underbalanced and whether single or two-phase fluid systems are going to be used. Something that often surprises people unfamiliar with CTD operations is how fine the cuttings are. This can cause challenges with solids control, especially when drilling is underbalanced, and must be taken into consideration when planning a CTD campaign. Completion equipment Ideally the formations drilled with coiled tubing can be left with a barefoot completion. Completion options are relatively limited when using a coiled tubing unit alone, unless using a hybrid unit. On land, it is usually simpler and more cost-effective to bring in a workover unit to run pipe. The challenge with underbalanced operations is to ensure that any completion run is installed whilst maintaining the underbalanced condition at all times Example planning process for an onshore mature field The following is an example planning process based on an onshore mature field where the original reservoir has been depleted:The operator may choose to sidetrack to access areas of virgin pressure away from the existing wellbores or can access other productive formations which are behind pipe. Whatever the target, certain aspects need to be understood which will be familiar to drilling teams everywhere. The formations between the casing exit and the reservoir need to be well understood. If there are particular zones that are troublesome, then now is the time to assess whether the kickoff point can be lowered to avoid the zone or if operational controls will need to be in place in the drilling program. The expected drilling fluids system should also be assessed at this stage as it defines the equipment requirements and has a significant impact on the well budget. This is also the time to evaluate the completion requirements with a particular focus on zonal isolation. For example, are there zones above that need to be isolated from the reservoir and, if so, can they be isolated with a swellable packer or is cementing required? Each consideration has a knock-on impact into the suitability of using CTD in either a managed pressure or underbalanced set up. Screening donor wells Assuming the subsurface objectives are broadly understood, the next step is to assess the existing well stock to see the wells that are suitable for sidetracking. These wells need to be screened for well integrity, current oil and gas production, location, casing/tubing size, and ability to reach directional targets. Once the initial list of wells has been created, then the available logs for each of the potential donor wells should be reviewed. The most critical logs are cement evaluation logs. Some older wells can be located on very small pads so the pad size for each well should also be considered and permission to extend sought if required. A minimum pad size of 200ft x 300ft is desirable but there is some flexibility depending on the equipment to be used. In some cases, it may simply be that the pad has not been maintained to its boundaries but the rights are in place and, therefore, it just needs to be prepared for the operation. The casing and cement integrity are both critical for successful operations. If a cement evaluation log is not available, then it should be planned to be carried out well before the CTD spread is to be mobilised, so that remedial cement jobs can be carried out if required. Ideally, casing pressure tests should also be carried out at this time to verify the integrity of the casing where the exit will be. Once the donor wells have been selected, the trajectories can be finalised and the wells permitted. To view the full article, please visit: World Oil or contact us
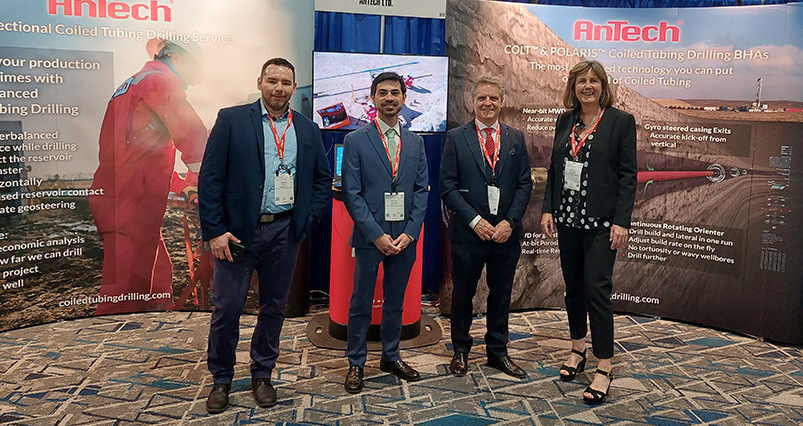
1649073600000
AnTech Exhibits at SPE/ICoTA 2022: Well Intervention Conference & Exhibition
AnTech were glad to be back exhibiting at the SPE/ICoTA Well Intervention Conference and Exhibition 22nd – 23rd March 2022, held at The Woodlands Waterway Marriott Hotel and Convention Center in Houston, Texas. Our team at AnTech were eager to be able to attend in person across the pond after last year’s virtual show together with the previous year having to be cancelled due to all the restrictions of COVID-19. We warmly welcomed two new members to our team who attended the show for the first time. This year, sponsors and attendees were finally able to network face to face and mingle around exhibitor’s booths once again. It was great for our team to be able to discuss and answer questions about Directional Coiled Tubing Drilling and our range of e-coil products in person throughout the show. As always, it was amazing to be able to attend the show and be a part of sharing and learning new industry knowledge together with our technical expertise. The AnTech team would like to thank everyone who stopped by our booth to have a chat with them. We are already looking forward to attending next year’s SPE/ICoTA Exhibition in The Woodlands. If you would like any further information or would like to know more about Directional Coiled Tubing Drilling, please contact us directly at ctd@antech.co.uk or visit our website.
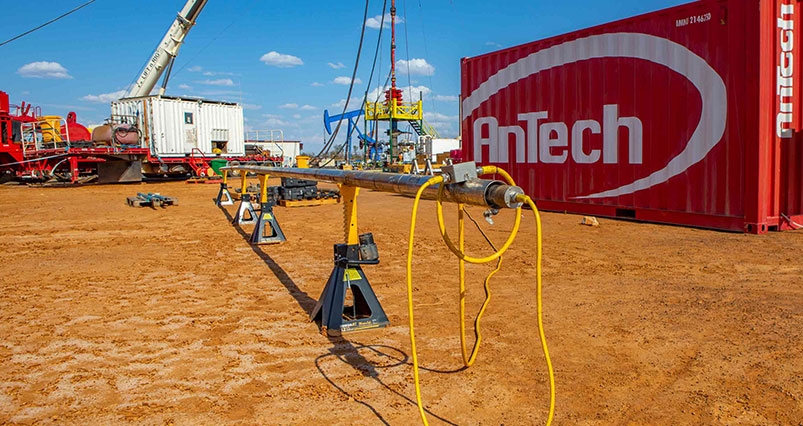
1648728000000
Tackling Efficiency For Cost Effective Re-entry Sidetracks, Using Coiled Tubing Drilling
Adam Miszewski, Global Operations Manager at AnTech Ltd talks tackling efficiency for cost effective re-entry sidetracks, using Coiled Tubing Drilling. Above: Fig 1. AnTech's COLT BHA and Workshop Container on site. Oilfield operations have been under constant economic and societal pressure to strip itself from unnecessary costs from interventions and become as efficient as possible. In the modern environment, producing the last drops from existing assets by re-entering and drilling laterals in existing wells is a pragmatic and economically advantageous approach if done cost-effectively. Coiled Tubing Drilling (CTD) is a technique that offers improvements in efficiency in many operational areas compared to conventional drilling but remains underutilized as a technique. This article describes how CTD technology can offer efficiency gains and cost reductions that operators can take advantage of. A track record of success CTD technology thus far has been widely used in two regions – Alaska and the Middle East. However, in lower 48 the technology is still underutilized and has not yet reached broader application. This article will summarize how bypassed reserves can be approached using CTD technology, often called Rigless Drilling. This technological approach not only provides an operational flexibility that considerably improves the prospects of success of drilling a new lateral wellbore in a depleted field, but it also often reduces a payback period that can be measured in a small number of months. One of the crucial advantages that CTD technology provides is its capability to drill in truly underbalanced conditions either through new wells or re-entry of existing ones. Drilling conventional wells with declining production in underbalanced conditions have proven to be very successful in the Middle East, where a number of CTD rigs have been slowly increasing over the last decade. Producers in the North Slope of Alaska can boast to be one of the most successful applicants of a low-cost method of re-entering old wells and increasing production using CTD, dramatically increasing the number of marginal barrels available to them. Figure 2 - Example CTD Wellsite layout Efficiency gains drive cost reduction There are two ways in which CTD can be more cost effective than conventional drilling. Firstly, in total cost per barrel which is less through a CTD re-entry than through a new infill well. Secondly, through a decrease in inconsistency in well costs due to the flexibility of coiled tubing. Minimal or no site preparation required – site prep is minimal for a CTD operation to be carried out.Low mobilization – Logistics of coiled tubing units is much more cost effective than that of a big drilling rig.Ability to deal with lost circulation – CTD fundamentally allows for managed pressure drilling operation even when not drilling underbalanced. The greater pressure control allows for losses to be avoided or reduced, however, when that is not possible, there is an option to allow losses and drill ahead unlike on a conventional drilling rig. The losses are also less costly in a lot of situations as a water-based fluid can be used instead of a more expensive oil-based mud.Tripping speed – Tripping speeds on CT unit are an order of magnitude faster than on a conventional rig. In formations that are abrasive, and therefore, require frequent bit trips, significant time can be saved on those trips when drilling with coiled tubing.Minimum time from decision to new barrels – coiled tubing is a call-off service and can be mobilized within a 24-hour notice. New barrels of oil can be brought to the market within a week allowing operators to take advantage of sudden price spikes and reduce their exposure to sudden moves down. There is a possibility to bring new barrels to the market while drilling if drilling underbalanced.Hybrid overbalanced/underbalanced – Some formations, such as the Buda and the Austin Chalk, have natural fractures that are extremely productive. Even though many wells will be drilled and never intersect a natural fracture, these wells might require hydraulic stimulation to achieve any meaningful production. However, when a highly productive fracture is intersected, lost circulation issues may arise. A conventional rig needs to remedy the losses by plugging up the fractures, meaning that any potential gain in production from intersecting the fracture is lost and the well would still require a stimulation. A CTD package allows the drilling process to be paused when a significant natural fracture zone is intercepted and switch over to underbalanced drilling – protecting the fracture, and therefore, increasing production from the well. Potentially even preventing the cost of hydraulically stimulating the reservoir. Operational Sequence Coiled Tubing Drilling can be applied to carry out complete well drilling operations, however, it can also work in combination with workover unit and wireline depending on economics of the project. Correct pre-planning and analysis of the availability of service providers in the area can bring many benefits in terms of operational time and cost. Overall steps: Pull upper completion/artificial lift. (Well dependent)Carry out casing exit above abandoned lower zone.Drill reservoir section with coiled tubing.Optional: Run liner/lower completion. (Well dependent)Optional: Install artificial lift. (Well dependent) Steps 2, 3 and 4 can be carried out using the CTD package. The other steps should be carried out by a workover unit. In locations where workover units can be mobilized at a lower cost, then it is possible to carry out the casing exits in advance ahead of mobilizing the CTD package. This ensures the CTD provider is only paid for when it is providing the maximum value. The most practical solution in North America is to carry out steps 1 to 2 with a workover unit on multiple wells prior to running a drilling BHA on a coiled tubing unit. Drilling open hole laterals with a CTD package can be as short as two to four days, total, depending on the target formation. So, it is possible to perform steps 4 and/or 5 with a workover unit following behind the CTD operation, therefore, having both service providers fully operational in tandem. It is prudent to run cost and service availability analysis prior to commencement of any drilling operation to find the best cost-effective solutions and reductions. Depending on location of the operation, various cost reductions can be found. Even if the reduction seems to be slim compared to the major costs, it can still have a significant impact on the total cost of the operation. Depending on a particular situation, it could be advisable to carry out non-drilling operations on a workover unit, yet, in some situations having a coiled tubing unit complete the whole drilling operation from the beginning might be the best solution. There are locations where it is feasibly cost effective to have two fluids return packages – as you are drilling on the first well, you can rig up the second and have the fluids package leapfrog from the first to second well, reducing the rig up time on each well and keeping the costs down. An unmatched capability to control pressures Since coiled tubing does not require any connections to be made, this allows the CTD application to be the only technology capable of controlling pressures at all times. Designed for underbalanced operations, CTD unit allows for downhole pressure to be managed as a standard with the utilization of a choke, allowing to quickly switch from overbalanced, managed pressure drilling operations to underbalanced operations. The limitations in the lateral length reach using CTD have now been substantially boosted with the assistance of a Continuous Rotating Orienter in the BHA and extended reach tools and utilizing larger coil diameters e.g., 2-5/8”. This progress has been demonstrated in a recent project on the North Slope of Alaska where lateral lengths exceeding 7,000ft were achieved. Figure 3 - Illustration of typical CTD Wellsite Equipment layout Equipment required for a CTD package Depending on the job requirements, equipment required for a CTD package may vary, but variation primarily comes from the fluids return side. If the job is going to be in an underbalanced condition, then a nitrogen unit can be easily connected to the pump, ready for a switch to two-phase drilling. Nitrogen pumps are easily mobilized in most locations in the United States allowing operational flexibility and keeping the costs down if there is a need for underbalanced drilling operations. A choke manifold is a standard component on all coiled tubing drilling operations that allows control of the bottomhole pressure. It is installed downstream of the BOP stack. Next piece of equipment in line is a separator. A simple mud gas separator is used in overbalanced operations and can be bypassed when dealing with well control situations. A more complex 3- or 4-phase separator can be put in line when there is a plan to go underbalanced. It can be rigged in from the beginning or drilling can be halted for placing it in. A gas flare should be installed at a safe distance linked up with a separator. Next in line are the fluid tanks that act as the pits. These can be simple open top frac tanks or the production tank farm, if possible. Usage of shale shakers is diminished due to small volume of cuttings on a CTD re-entry job. Most of the time the cuttings will settle out in the separator or in one of the frac tanks. A weir tank which has baffles installed in the tank to assist with separation of the cuttings can be used if separators are not utilized. A centrifuge is then connected to the final stage to remove the remaining solids before recirculating. Depending on the desires of the operator, the mud can be either bought pre-mixed or a mix tank can be included in the tank/pit structure to mix a simple, solids free mud, which can then be moved and used on the next well after completing the first one. This would require the mix tank to be set up only once. Considerations for drilling fluid Drilling fluids can be another cost saving factor when using CTD drilling. Predominantly the required fluid is simple, solids free, such as inhibited brine with polymer that is standard for overbalanced or managed pressure applications. Compared to drilling mud used on conventional rigs, this type of drilling fluid should be significantly lower cost. If there are any fluid losses during the operation, this in turn, also minimizes costs associated with that. During an underbalanced drilling operation, a single phase or a two-phase fluid can be utilized. The reservoir pressure and well design program will define type of fluid that is going to be circulated. Single phase fluids for underbalanced drilling are water, brines, oil, or diesel usually. Each one of those can be lightened further by pumping nitrogen at the same time. Another benefit of running a CTD package can be found in reservoir damage issue. By drilling underbalanced, an operator can substantially enhance the production and avoid any skin damage/plugging, eliminating the need for the costly stimulations, even if it initially seems that drilling with single-phase fluid is less expensive. However, looking at final economics and results can have a much higher benefit in the end. Considerations for BHA Reducing rig up and deployment times are essentially important. One of the two important considerations when choosing a bottomhole assembly (BHA) for CTD is the total length of the BHA. Deploying the entire BHA above master valve can only be achieved with a short enough BHA. The sequence would then start with placing the BHA in a mousehole, and bringing the injector and lubricator held by crane over the mousehole to suck in the BHA into the lubricator upon connecting it to the coiled tubing pipe and wireline via a cablehead. The Injector and lubricator with the BHA inside of it are then moved over the well and BOP connections are made up. This makes the deployment safe and fast, avoiding any need for a tower or pressure deployment. The second important consideration to account for is the tortuosity of the wellbore, in other words, how straight the drilled wellbore is. The straighter the wellbore, the deeper the operator can drill and avoid any possible tubing lockups and it also eases running the completion to target depth. A perfectly straight hole can only be achieved by using a continuously rotating orienter that can rotate clockwise or anti-clockwise without any need to stop the drilling process. Having an orienter module with such capability also maximizes the weight on bit (WOB) which helps to drill a long lateral or a shorter one with high ROP. Figure 4 - Coiled Tubing Drilling equipment Case Study – Austin Chalk Austin chalk is a well-known reservoir which has a fantastic history of being a major producing field for many years. All wells targeting the Eagle Ford Shale will pass through the Austin Chalk. Now, as the number of wells in the Eagle Ford that are reaching the point where they will need to be abandoned is increasing, it is feasible again to use the existing infrastructure already in place and re-drill Austin Chalk reservoir to take advantage of any additional barrels that can be brought to the market. One of the biggest challenges of drilling the Austin Chalk for many years used to be fluid losses. It is a highly fractured reservoir where large fractures can be intersected resulting in significant losses of the drilling mud. These losses can add up to a significant fraction of the well cost as the oil-based mud is quite expensive. Operators have to consider these possible losses when budgeting for the year, however, reducing the variability in mud costs would allow the operator to use its capital more efficiently. Using a CTD package, an operator can achieve higher control over pressures because of the choke and also use simpler type mud fluids. For example, a solids free brine, such as 4% KCL brine-based mud with xanthan gum as the viscosifier and starch for filtration control would be suitable. This type of fluid weighs around 8.6-9.0ppg and in case, any additional pressure is required to exceed the reservoir pressure, it can be applied at the choke. The choke can be opened when circulating pressure needs to be brought closer to the reservoir pressure to lessen the losses. The choke can even be closed for a period of time until the losses are cured. When it comes to pressure control, the flexibility and adaptability on coiled tubing is considerably more than on a conventional rig. When a highly permeable fracture is drilled through, a circulation issue may arise, so switching to underbalanced drilling as soon as that happens, would solve the fluid losses issue, and protect the productivity of the fracture. This alternative strategy allows the formation to be protected from damage and the production to be maximized by drilling underbalanced. In case, no fractures are detected, then the well can be drilled as normal at a low cost without the use of nitrogen equipment. It is highly possible to achieve a lateral length of over 7000 ft in the Austin Chalk formation utilizing the suitable equipment and designing a comprehensive drilling plan. To view the full article, please visit: World Oil or contact us
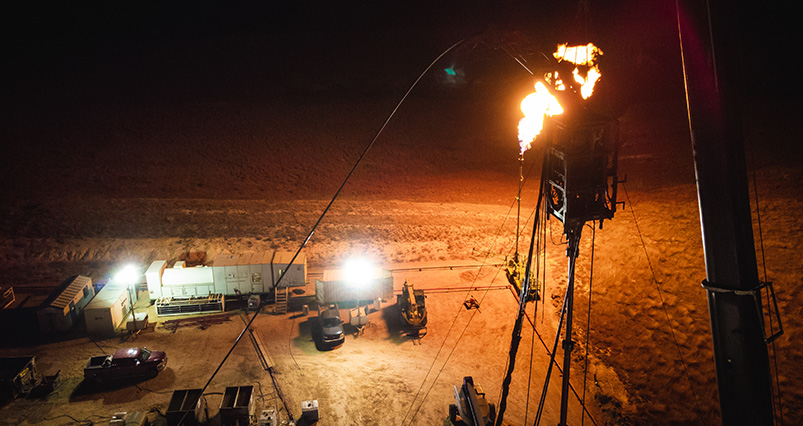
1631112381000
The Time To Choose: The Importance Of Feasibility Studies In Coiled Tubing Drilling
Adam Miszewski, Global Sales Manager at AnTech Ltd discusses the importance of feasibility studies in Coiled Tubing Drilling. Above: Fig 1. AnTech on an Underbalanced Coiled Tubing Drilling operation in Texas. Learning on the job is a great way of gaining experience but I think we would all be surprised if an airline pilot hadn’t spent some time on a simulator before flying passengers. The reason is that the cost of failure, crashing, is expensive in both human and financial terms. It is much better to simulate events offline. Oilfield operations, where high pressures, hazardous chemicals and complex systems are involved are no different. Digitally simulating oilfield operations ahead of time saves cost, prevents accidents, and speeds operations. That is why feasibility studies are so important. The key to getting the most out of technology is understanding when not to use it. After all, the most advanced and cutting edge technology in the world is useless to us if it is not used within the correct application. This is especially the case for broad use technologies like Coiled Tubing Drilling (CTD) that can be employed in a range of applications, but are complex in their specifics. For example, CTD can be a low cost solution in some applications, while in other applications it requires larger investment in order to achieve a larger reward. In remote operations CTD has the advantages of low mobilization cost and a small crew requirement, which maximizes ROI by delivering the same production as a conventional rig at a lower overall project cost. However, when drilling a depleted reservoir underbalanced with two-phase fluid system of water and nitrogen, the spread rate can be higher than a conventional rig operation but the return on investment is realized through achieving production levels that could not be achieved using a conventional rig drilling overbalanced. A sales representative selling a broadly applicable technology such as CTD can seem disingenuous by listing all the potential benefits of the technology, because while these benefits are achievable in the broadest sense, the end client may not actually realize all of the benefits in every application. It is a case of identifying that the right technology is being used in the right configuration in order to maximize value to the end client. Therefore, any high quality feasibility study must take into account both technical and commercial feasibility. Figure 2 - BHCP and Gas Production sensitivity to Productivity Index To illustrate this point for the sake of this article, we will focus on the fundamental steps and points of consideration that would be undertaken during a feasibility study for gas wells being re-entered and drilled, the assumption being that the well should be drilled underbalanced with coiled tubing in order to avoid formation damage, as well as to maximise productivity from the well. A feasibility study can be thought of as a “negative proof”. In maths, a negative proof is a demonstration that a particular problem cannot be solved as described in the claim. In this case, the claim is that drilling the well using CTD is the technique most likely to maximise success and return on investment. In actual fact, a “feasibility study” is quite the opposite of how it sounds, because while something can be feasible, it may not always be desirable given the specific circumstances, and to ignore that fact would be a disservice to the end client. On this basis, the first step is to discuss with the client their rationale for wanting to apply the technology to their field in the first place. The operator understands their fields and their operational challenges better than anyone and they will have been attracted to the technology based on solving specific problems. A quick phone call can often be enough to gauge whether or not there is a suitable application for CTD or not. At this point it is also important to answer a few basic operational questions, such as identifying any access restrictions, determining the size of the pad, and describing the general drilling experience in the target formations. Assuming the project still looks attractive after that first discussion, the next step is to identify the level of detail required from the study, which will determine how deep into the technical analysis to go. Some operators may want an answer as fast as possible whereas others may require more detailed analysis, even if the result is that the specific project or well is indeed not feasible. This may be due to the fact that they wish to build institutional knowledge around the technology and understand how to evaluate their other assets in-house in order to make best use of the benefits of the technology. Figure 3 - Operating envelope analysis. Tubing performance and Productivity for one operating condition. The core advantage of coiled tubing when drilling is pressure control. Continuous pipe and equipment rated for 15,000 psi wellhead pressure as standard gives a lot more flexibility in terms of drilling both underbalanced and at balance with formation pressure. When drilling underbalanced or at balance on a conventional rig, the rotating control device (RCD) has a much lower pressure rating than the rest of the pressure control equipment. A standard RCD has a pressure rating of 2,000psi static, 1,200psi when stripping and even less when drilling ahead. However, on a coiled tubing unit the rotating control device is replaced by a stripper that is capable of operating up to the same pressure as the blow out preventers in most instances. UBCTD has the safest possible set up from a well control stand point. Also, this means that there is much more scope to adjust the well parameters on the fly based on live observations while drilling the hole section. For example, when drilling through a highly productive fracture. The drilling choke is another key piece of equipment on a UBCTD project. Flow from the well is controlled through the circulating fluid and the back pressure provided by a choke. Chokes can be remote controlled and manual or automatic. There are four major components to a UBCTD feasibility study: wellbore hydraulics modelling, coiled tubing modelling, equipment specification and cost estimation. Prior to working on any hydraulics modelling, a draft trajectory should be made. The trajectory will produce the first set of questions to be answered, which will constrain the well design. For example, can the well be sidetracked and landed within the target formation, or are multiple formations drilled through? Any formation drilled through must be assessed for wellbore stability, and it must be determined whether or not the formations can be safely in communication with each other. At this stage it will also be possible to start making an assessment of total project length, and therefore budget, which can be refined as the hydraulics modelling progresses. Once the trajectory has been designed, the hydraulics models are built in a steady-state multi-phase flow modelling software and a critical factor analysis is carried out. This will give an idea of the fluid type and weight that will be used. At this stage it is important to determine if a single phase fluid such as water or brine will be used, or a two-phase fluid such as co-mingled water and nitrogen. Once the critical factor analysis modelling has progressed to such a point where some certainty is known about the operational limits of the fluid type and weight and the well productivity, then a tubing forces analysis can be carried out in order to understand the coil size required to achieve the target lateral length. The design of the coiled tubing effects the hydraulic response of the well and vice versa. For example, a larger outer diameter of the coiled tubing will reduce the annular space and therefore increase the bottom hole pressure and the annular velocities, both of which are critical factors to consider in the well design. However, from the other analytical perspective, the injected fluid and the produced gas volumes will effect buoyancy, annular pressures, and pump pressures, which will in turn effect the buckling limits, available weight-on-bit, lateral reach, overpull and coil life. Once a coiled tubing size has been selected, the models are run in order to determine the relationships between injected fluids, reservoir productivity, circulating rate and wellhead pressure. The primary concern is to address how the well can be kept safely under control during the entire operation. In underbalanced operations, the primary well control is provided by a combination of flow and pressure control equipment and secondary well control is provided by the BOPs. Therefore, understanding the potential gas production is important for understanding controllability, fluid and equipment requirements in order to drill the well safely. In the feasibility study stage it is particularly important to focus on the extremes. Figure 1 shows analysis at a range of productivity indices, Figure 2 shows tubing performance and productivity for one particular operating condition, and Figure 3 shows how well production varies with pump rate and wellhead pressure. Coiled tubing has a distinct advantage in that once stable circulating parameters are obtained then they may be able to be held steady for the entire hole section. This is very important in gas systems where transient effects are difficult to control but also it prevents overbalanced situations inadvertently occurring and minimizes the chance of hole collapse through varying wellbore pressures. One question that may not be intuitive to those not familiar with underbalanced drilling is that, as with the coiled tubing string design and trajectory, there is a limitation on achievable lateral length due to the wellbore hydraulics. It is possible to be underbalanced at the heel of the well and overbalanced at the toe. This is an important factor to take into account as it is possible to take losses or overpulls at the toe due to poor hole cleaning when the well is producing as expected from the heel. This can be controlled to a certain extent through operational procedures, e.g. flow rates and optimized fluid weights, and well design e.g. hole size and casing size. It is clear by now that the nature of UBCTD feasibility studies is for an iteration of the models and design considerations. However, slowly but surely the critical factors are narrowed down. Once the hydraulics models are at this stage then the coiled tubing models can be revisited for optimization. With the combination of the hydraulic and coiled tubing models the final achievable lateral reach and well productivity can be calculated. An expected coiled tubing grade and draft design should also be specified at this stage as it is important both from an engineering stand point but also cost and durability stand point. One thing that has not been mentioned so far but is critical throughout the analysis consideration must be given to what would happen during real life operations. A model will provide a solution but experience must determine if that solution is achievable using the equipment and personnel available. “What if” scenarios need to be addressed in the feasibility study, although not in great depth. It is important that the ability to deal with the unexpected is taken into account from the beginning, especially in terms of safe operations. Figure 4 - Production Contour In terms of the equipment required for a UBCTD campaign, the major components are the coiled tubing equipment including pumps, the returns system (e.g. fluids, solids, and gas handling) and the directional package. When drilling with a two phase system, e.g. water and nitrogen, there will be additional pumps, storage tanks and logistics. If the intention is to push any produced gas to the sales line then consideration must be paid to the maximum nitrogen content allowed and maximum line pressure. To view the full article, please visit: Oilfield Technology or contact us
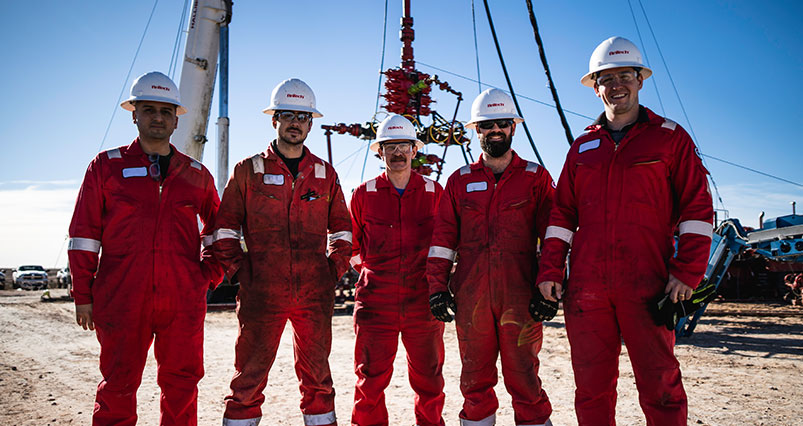
1617019200000
AnTech Exhibits at SPE/ICoTA 2021: Well Intervention Conference
AnTech exhibited at the SPE/ICoTA Virtual Well Intervention Conference 22nd – 25th March 2021, normally held at The Woodlands Waterway Marriott Hotel and Convention Center in Houston, Texas. Our team at AnTech were pleased to be able to support this year’s virtual conference after last year’s show was cancelled due to the restrictions of COVID-19. This year, sponsors and attendees networked virtually in the ‘Sponsor Zone’ and people visited us ‘face to face’ by making an appointment to chat on-line and ask questions about Directional Coiled Tubing Drilling. Adam Miszewski, AnTech’s Global Operations Manager, presented at one of the Technical Sessions: SPE-204418-MS Underbalanced Drilling with Coiled Tubing: A Case Study on the Alaskan North Slope, which Proves the Benefits of Drilling a Straight Hole. The paper received a good turn out and had many interesting questions after the presentation. Although it was very different this year for everyone, it was great to be able to sponsor the show and still be a part of sharing and learning new industry knowledge. The team would like to thank everyone who got in touch and are looking forward to attending next year’s SPE/ICoTA Exhibition in The Woodlands. If you would like any further information or would like to know more about Directional Coiled Tubing Drilling, please contact us.
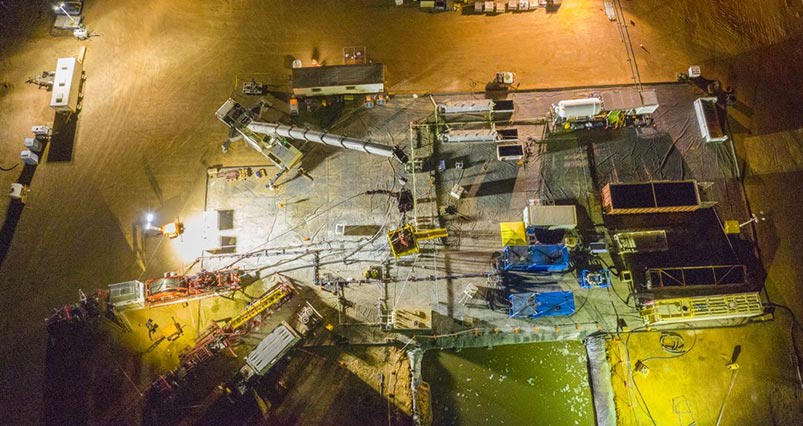
1616673600000
Addressing The Re-Entry Problem Of Barefoot Multilaterals On Coiled Tubing
Adam Miszewski, Global Sales Manager at AnTech Ltd addresses the re-entry problem of barefoot multilaterals on Coiled Tubing. Above: Fig 1. A multi-lateral UBCTD re-entry operation and equipment at night The drilling of multilateral wells that connect to the main motherbore has been common practice since the early 1990’s as a means of maximising well production. By accessing numerous production zones and increasing the reservoir contact of each well, multilateral well designs are able to boost production with minimal additional drilling and completion costs, Fig. 1. This has been shown to be particularly beneficial in an offshore environment where well slots are limited, there are also significant advantages onshore, where the use of multi-lateral wells can significantly reduce the environmental impact in comparison to drilling multiple wells. The advanced technology and expertise required to drill and successfully complete these wells are these days well understood. However, the ability to re-enter a chosen lateral successfully on the first attempt, and to quickly and positively validate that entry, has not advanced at the same pace. Most multilateral wells have horizontal or near horizontal reservoir sections which require coiled tubing in order to re-enter. As such, coiled tubing drilling (CTD) has been integral to multilateral well design since its inception. A typical multilateral well is shown in Fig. 2.Figure 2 - Typical multilateral well profile drilled conventionally and on coiled tubing CTD has long been proven as a highly successful, cost-effective method of re-entering old wellbores and accessing bypassed and attic reserves, thus revitalizing depleted wells and providing operators with a high return on investment in their mature assets, Fig. 3. As well as optimizing well lifetime, CTD technology offers the opportunity to drill underbalanced, maximizing oil and gas production per section of formation drilled (see Fig. 1 on location). Incorporating effective multi-lateral well design into CTD operations can increase profitability even further by maximizing the length of productive reservoir rock drilled per motherbore. This combination of oilfield technology has been shown to be very effective in many locations, but most significantly in the UAE, Saudi Arabia and Alaska, USA, with many papers published detailing the benefit to the operators’ bottom lines. Figure 3 - AnTech CTD field crew on location for an UBCTD job in Australia The stimulation of intervention operations that an operator may wish to undertake on an individual lateral are no different from the stimulation of a single wellbore in a conventional completion, except in regards to lateral entry and consideration of the interaction between laterals during stimulation. The greatest challenge and potential barrier to increasing multi-lateral applications is the difficulty in entering a specific lateral first time and then positively confirming which lateral has been entered. With open-hole side-tracks in a horizontal section, the lateral will drop down, making it impossible to enter the original lateral with a drilling assembly. Even a motor on a maximum bend setting will not be sufficient. Hydraulic systems The most commonly used method for accessing the desired lateral is to utilize an indexing tool and pressure-actuated knuckle to kick off. An indexing tool works by rotating the BHA by a set amount as pumps are cycled. In other words, pressure is applied through pumping, released by stopping pumps and then re-applied through re-starting pumping. With certain tools, the degree of rotation on each pressure cycle can be set on surface prior to running in hole. A pressure actuated knuckle kicks off a bullnose beneath the knuckle, at a set angle, by using a differential pressure across the knuckle. It is essential that the knuckle and the length of bullnose are sized according to the BHA size and hole geometry. Due to the reduction in flowrate through the tools while the knuckle is in use, the BHA will usually include a pump-out choke, which can be sheared out once the chosen lateral has been located in order to enable higher flowrates for cleaning out the well. The procedure for utilizing a pressure-actuated knuckle system is to run in hole until the BHA is past the kick-off point or junction. The pumps are then started, and the BHA is pulled out of hole slowly. As both the knuckle and bullnose are in the motherbore at this point, the bullnose cannot fully kick off. This causes a high differential pressure, which will be indicated on surface as higher pump pressures. If the knuckle has been oriented correctly, then as the BHA is pulled out of hole while pumping the bullnose will kick off by the maximum degree into the lateral, and bleed ports will be opened. This will result in a reduction in pressure across the knuckle and provide a positive indication at surface that the window has been found. If no pressure drop is detected at surface, then the process is repeated (possibly multiple times): run in hole with pumps off, start pumps, indexing tool rotates knuckle and bullnose, pull out of hole slowly to find lateral. In some cases, the only way to be confident that the correct lateral has been entered is to run to bottom and tag well total depth.. The hydraulic solution is one that many service companies are familiar with and have access to. Its advantages are that it only uses a standard coiled tubing unit and pumps that require very little specialist crew training, and this equipment is not affected by temperature limitations. These benefits make the hydraulic system the most cost-effective option on a day rate basis. However, what is gained through lower day rates can be lost easily through additional unproductive or invisible lost time spent attempting to confirm entry into the lateral, which may also result in loss of fatigue life of the coiled tubing. Additionally, it is very challenging to work with any logging tools using this solution, as they need to be flow through and run in memory mode. Finally, every time the pumps are cycled there is a risk of experiencing issues such as stuck pipe or collapsed tubing. Electrical systems Increasingly, coiled tubing operations are moving to smart systems, with the implementation of real-time measurement functionality on every run-in hole. These systems use a wireline inside the coiled tubing, often referred to as e-coil, to power and communicate with downhole tools from surface. This provides the advantage of high data rates, even when drilling with a gaseous fluid, such as a water and nitrogen mix or mist drilling. Moreover, it enables real-time measurements, such as weight on bit, pressure and temperature, in addition to casing collar locator and gamma ray sensors for depth correlation. Certain systems have the capability to run on hybrid cable, which contains both conductor and fiber optic, providing additional capabilities in distributed temperate and acoustic sensing. Utilising these systems can result in substantial improvements to operational efficiency from. It is common practise for the directional drilling service company to take responsibility for all aspects of the wireline. As such, coiled tubing crews must include personnel with specific e-coil expertise. However, in order to achieve a greater uptake of wireline-enabled coiled tubing operations, service companies will need to ensure that training also provides coiled tubing crews with an understanding of the other service line, defined roles and responsibilities on the wellsite, data integration between the service lines, and an efficient operational set-up. Operators that adopt e-coil intervention operations can expect more-effective interventions that take less time and cost less than standard coiled tubing interventions. Moreover, for service companies that can offer an effective and seamlessly-run package, the result is a substantial improvement in market share and revenue, as well as greater employee engagement through a broadening of skillsets and experiences. Electrical multilateral re-entry tools When it comes to electrical multi-lateral re-entry tools, there are unfortunately very few options on the market at present. The first electrical system to come to market used a sensor to locate the window as the BHA was run past it. Once the BHA had passed the window, and the window orientation had been identified, the BHA was pulled out of hole to a location above the window. An electrical kick off knuckle was then oriented and kicked off, and the BHA was run back in hole. This time, the kick-off knuckle would guide the BHA into the lateral. The market is beginning to see a new wave of electrical multi-lateral re-entry tools rooted in directional coiled tubing drilling (DCTD) technology, which has been successfully used on e-coil around the world for the past 20 years. Most wells drilled with coiled tubing are re-entry wells and are drilled underbalanced, where the reservoir pressure is higher than the borehole pressure. By re-entering old wells, operators can target bypassed reserves using pre-existing top hole and surface infrastructure. Drilling underbalanced offers the operator the advantage of zero formation damage in the new hole section, which is particularly important in mature fields with declining reservoir pressure. However, drilling in underbalanced conditions, often with two-phase drilling fluids, is extremely tough on downhole tools, due to the vibration and associated compounded temperature challenges. A DCTD BHA is equipped with the standard sensors and drilling modules required for intervention operations, along with the full range of measurement-while-drilling (MWD) directional sensors. The crucial component of a DCTD BHA, however, is the orienter. When drilling wells conventionally with a bent sub motor, the orientation of the motor, or toolface, is set from surface by rotating the drill pipe. Drilling ahead with a no drill pipe rotation is known as a slide and will angle the wellbore in the direction of the toolface. When the well trajectory requires a straight, tangent section, then the drill pipe is continuously rotated while drilling ahead. DCTD uses the same principle, but because the pipe cannot be rotated from surface, the toolface must be set downhole using an orienter. The orienter is controlled from surface via the wireline, which makes it possible to communicate and power the BHA, even when drilling with air. The new generation of multi-lateral re-entry tools operate using the sensor package and downhole orienter of the DCTD BHA, combined with an electrically operated bent sub (EBS). The EBS can be set to the desired angle and activated from the surface. The procedure for selectively entering a lateral is as follows: as the BHA is run in hole, gamma logs or the casing collar locator (CCL) are used to correlate a depth as near to the window as possible. Once depth has been confirmed, the EBS is oriented as per the well surveys and the as-drilled slide sheets created by the directional drillers when the lateral was initially drilled. The EBS then can be activated as the BHA is slowly run in hole. As the BHA is run into the sidetrack point, the EBS will pick up the desired lateral (as shown in Fig. 4). Figure 4 - Re-entry tool Gamma, CCL and inclination measurements can be used to confirm the lateral entry, and in open-hole sidetracks, the azimuth measurement also can be used. This makes it unnecessary to run to the bottom of the lateral in order to identify which lateral has been entered. Crucially, the use of a fully electric system makes it possible to enter and confirm the lateral on the first attempt, resulting in significant savings in operational time and cost for the operator. To view the full article, please visit: World Oil or contact us
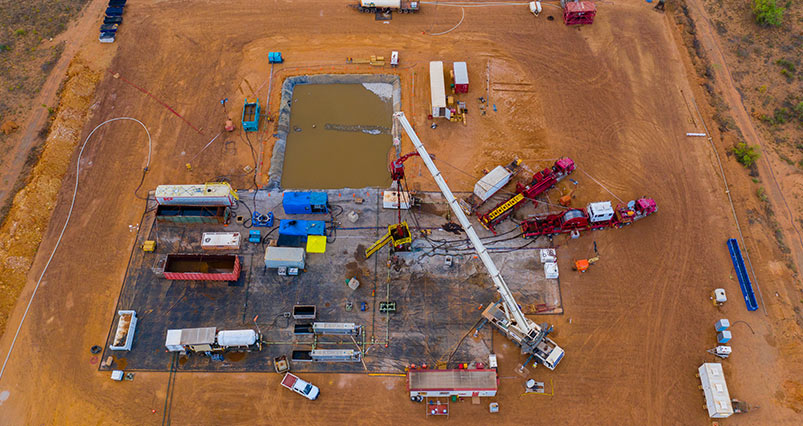
1585742400000
Underbalanced CTD System Uses Internet Technologies To Ensure Reliable Data Handling
Wellsite IT has evolved dramatically since the days when seeing a laptop on a wellsite was a rare occurrence. It has needed to. Today’s technically advanced drilling techniques use high data volumes from multiple data providers, meaning reliability and security are more important than ever. By Toni Miszewski, Managing Director at AnTech Ltd. For a recent Underbalanced Coiled Tubing drilling (UBCTD) job in Western Australia it would have been perfectly possible for a directional driller to have steered the directional drilling assembly from the comfort of an office in the UK over satellite internet. Whilst this might not be desirable for a variety reasons, it shows the capability of modern communications and computing systems. The same internet technology that makes ecommerce and online banking possible can be applied to high data rate oilfield applications because the fundamental requirements are the same. Namely, to provide timely, reliable, secure data to remote users. In place of static web pages, the most useful web applications that people are familiar with, deliver data from databases. This mirrors what happens in high data applications such as UBCTD so the same technologies can be used. Another feature of the internet is that servers in data centers are managed remotely so there is software specifically adapted to configure and monitor and control hardware at a distance. This is exactly the capability that is beneficial in the oilfield where the field hands often don’t have advanced IT skills and, even if they did, they don’t have the time to put them to use, because that is not their primary task. Most applications are not as data intensive as UBCTD so if high data applications can be made to work effectively, the same technology can work for simpler applications. To get an understanding why UBCTD is so data intensive, it is worth thinking for a moment about the measurements being acquired. In these systems, data from downhole comes up at electric wireline speeds rather than slow mud pulse speeds – it is also transferring data from up to 200 sensors at any one time. This downhole data has to be combined with surface data from the CT rig and the flowback equipment in real time. Add in the complication of these data points being controlled by different providers and you start to understand the processing power required. In short, it means that ad hoc methods of data transfer are no longer viable. The development of wellsite IT over time Before the advent of the PC, the most sophisticated piece of IT at the wellsite was the wireline logging truck. As PC technology became more widespread, PC’s appeared on wellsites for reporting, email and data acquisition. From the first time someone took a computer to a wellsite, the industry has always been keen to harness what technology has to offer. However, the evolution has not been without its problems and in many cases the solution has been an ad hoc fix rather than a high-quality strategy. Everyone has a tale to tell about IT at the wellsite. There are the practical issues. Wellsites are rugged environments that require robust equipment. Consumer grade equipment is so much cheaper and readily available than specialist ruggedized equipment, so it gets used in preference. But dust and other contaminants often shorten the useful life of consumer grade equipment. It’s difficult to remember the day when not everything was WiFi enabled. Cables were strung across the wellsite and how many hours have been lost repairing a communications cable that has been damaged by a truck driving over it? When WiFi did become available, many of us will be able to recall instances where the source of a slow-running communication link was tracked down to a crew member streaming video on their mobile phone. Made possible because the network password was shared more widely than intended. Then there’s what happens at the end of a job. With data stored on desktop computers, it’s all inaccessible between the time it’s packed up and the time it arrives back at base losing valuable post job processing and reporting time. These delays create inefficiency and cost money. These are all signs of an IT system under limited control with all the associated security risks and performance issues. This is not a desirable or efficient way to operate and with readily available technology things can be improved dramatically. Figure 1: AnTech's COLT BHA and workshop container, on site in Australia. How internet technologies help The internet is an integral part of modern life. It has been able to become so pervasive because of its speed, reliability and ubiquity. Long gone are the days of dialling up over a phone line and logging into a single server which would display static web pages. Now it is all about load balanced server farms, redundant databases that power ecommerce and network switches that efficiently and quickly connect New York to London and to Tokyo without any extra effort by the user. A lot of time and billions of dollars have been spent to improve the technology necessary to enable companies to move their business online. For this to have happened the IT tasks that keep the system running have had to be automated. A feature of the way that the modern internet is managed is that the person doing the managing is very rarely anywhere near the physical hardware being used and the end user needs almost no understanding of the technologies to be able to use its functions. In oilfield terms, the wellsite crews are the equivalent of consumers who want to take advantage of IT, not run it. This has been made possible by having many applications run directly on the web through a browser without having to download any extra programs to their device. These so-called web apps can be updated centrally, and all updates are available to end users at the same time. This same concept can be applied to the wellsite by putting a mini data center at the heart of the wellsite IT system and ensuring that there is reliable connectivity to it. With the mini data center, on-site quality-of-service to local users is maintained, and with a good internet connection, it essentially becomes another part of the cloud for the purposes of management and remote data processing. The WellVault™ mini data center at the wellsite The journey to a better wellsite IT system is to treat it as an integral part of the wellsite, central to the way that the wellsite operates rather than as an added productivity tool, added later. In a UBCTD setup, the time between rig up and rig down is relatively short, a few days, and there is no existing installation such as a rig communication system to plug into. Even if there was, it wouldn’t necessarily be configured for the large amounts of data that are part of an underbalanced drilling operation. Figure 2: The WellVault mini data center setup. Environmental protection: Heat, cold, water, dust and vibration are the enemies of delicate IT equipment at the wellsite. These can all be addressed but sometimes the measures conflict with each other. For example, one good way of combatting the effects of dust is to specify fan-less computers. But all computers generate heat so the fan-less feature may have been made possible by slowing the computer clock speed with a knock-on effect on performance. So, if performance is critical, it will be necessary to provide dust protection and filtering for fan cooled computers. Protective cases can isolate equipment from shock and vibration in use and during shipping. Internet connection: Each location will have an optimum way of connecting to the internet be it via satellite, mobile internet and in some cases microwave link. What is essential is that the connection is planned and tested rather than being considered as an afterthought or nice-to-have feature as may have happened in the past. Data interfaces and displays: Individual data displays are placed around the wellsite to provide the communication required for an integrated operation such as UBCTD. These also serve as a connection to third party data sources and the driver of the WiFi access points. Long range point-to-point WiFi: Specialist WiFi access points provide longer range than consumer items. The biggest challenge here is to be able to offer a range of secure fixing methods to be able to place them as required, preferably on the outside of cabins with reliable cable entry into the cabin. Remotely configurable routers: To ensure equipment can be monitored and maintained remotely to avoid costly downtime, every device needs to be configurable remotely. Consumer products are readily and cheaply available, but they do not give the control of configuration or the feedback of data required for a remotely controlled industrial system. On the other hand, enterprise-grade devices do offer the level of configurability and data feedback required. Redundancy: To ensure reliability, especially in situations where there is limited IT knowledge on site, a robust redundancy setup is required. This means at least two servers operating concurrently, one as a backup, so that in the event the first server goes down, operation can switch to the backup servers without a loss of data. Currently, the switch over is made with the intervention of a remote engineer, but newer technologies exist to enable the switch over to happen automatically without any human intervention, potentially removing server failure as a cause of any downtime. Encryption and access control: When it comes to information security, end-to-end encryption is essential and each device has to have its own firewall and anti-virus software. To prevent the system being used by crew members for non-operational reasons, access should be limited using IP address control. To view the full article, please visit: World Oil or contact us
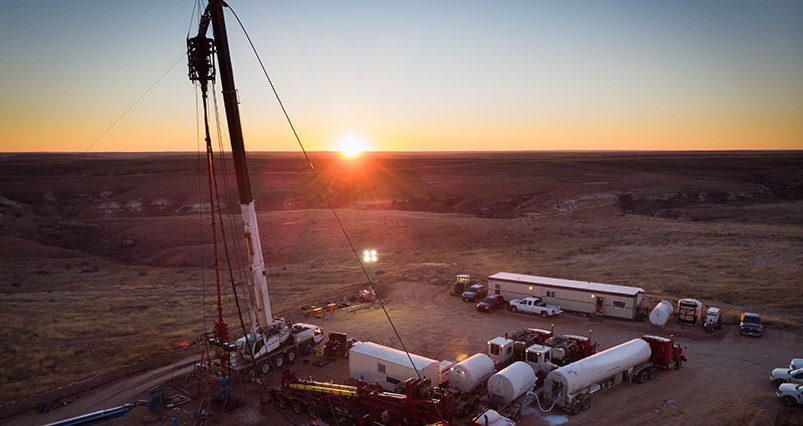
1580558400000
Maximising Returns From Declining Fields Using Underbalanced CTD
A recent project in the Texas Panhandle shows how the latest technologies and collaborative working offer an exciting way forward for the industry. By Adam Miszewski, Global Operations Manager at AnTech Ltd. As the industry matures, maximising the value that can be captured from known reserves is more important than ever. However, in declining fields, both operational and cost effectiveness need to be exemplary if production levels are to return a viable profit. There is much to be said for marginal gains – the practice of making the tiniest of tweaks that, when added together, deliver a significant improvement on standard ways of working. But approaching a project from a completely new angle can also deliver the required results. This was demonstrated in a project in the Texas Panhandle where new technologies and new ways of working delivered increased production rates at reduced cost when compared to traditional methods. Project background The project was a two well re-entry campaign in the Texas Panhandle. It was part of a wider campaign to intercept fractures and access untapped reserves to boost production and revitalise a field that had not been producing for many years. The two wells were primarily gas producers, with condensate and water also being produced. Both wells were to be drilled underbalanced to reduce formation damage and to avoid significant impact on subsequent production. Underbalanced Coiled Tubing Drilling (UBCTD) was seen as the best way to drill the reservoir because it provides continuous stable underbalanced bottom hole pressure, as well as fast, safe and effective operation with two phase drilling fluids. Figure 1: The interaction of service companies for the UBCTD campaign in the Texas Panhandle. New technologies In the early stages of the project, it was decided that wellsite data acquisition, offsite support for data analysis and information from downhole sensors would be aggregated and shared with all parties in real time. Doing this would mean all parties would always have a complete, real time picture of what was happening on the wellsite, enabling rapid decision-making. Having the data in real-time would also allow the use of RockSense, AnTech’s proprietary synthetic porosity algorithm, which distinguishes between different formations by combining downhole and surface data in real time to give an at-bit measurement of porosity. It offers two considerable advantages over traditional geosteering techniques. First, wired telemetry has a high data rate, so multiple measurements can be made for every foot drilled and operators can gain inch-level resolution. Second, because the data delivered is representative of conditions at the bit – not 20-25ft behind it – the driller can deliver an optimally placed wellbore, with more feet drilled in the target zone. New ways of working To allow real time data aggregation, a much more collaborative approach than is typical, was needed. Usually, the four principal parties in a UBCTD campaign (the directional downhole tools provider, the coiled tubing service company, the underbalanced drilling fluids package and the operator) each uses their own data acquisition system. In this scenario, an incomplete picture is available to any party at any given time and there are delays in decision making while data from the other parties is requested, collated and analysed. In this project, AnTech, the directional service provider, took on the role of aggregating the data. In advance of arriving at the wellsite, they provided the conversion kit to convert the rig to e-line (slip ring collector, collector bulkhead) and enable the CT unit to run e-coil. AnTech also provided pre-job engineering, pre-job project management, and the downhole equipment. Halliburton provided the CT unit and pumps, ADA provided the fluids separation package and Blade Energy Partners provided pre-job engineering and wellsite supervision/project management on-site. (See Figure 1.) To view the full article, please visit: Oilfield Technology or contact us

1569240000000
AnTech Holds International CTD Training School
AnTech ran a widely diverse training school in Exeter to provide the practical knowledge of the company’s owned forefront Coiled Tubing Drilling technology. AnTech recently held a training school in their global headquarters in Exeter in view of winning two major Coiled Tubing Drilling (CTD) operations in Alaska and Australia. The successful completion of those drilling campaigns is the main goal of the company this year. The effort that AnTech put in the realisation of the training school was a crucial factor in the achievement of that goal. AnTech gathered at their Exeter headquarters 10 newly hired employees and contractors with the aim of giving them all customised expertise necessary for the successful completion of the scheduled CTD operations. The new staff were trained on the cutting-edge drilling technology designed and manufactured by AnTech in Exeter and the operational aspects of running the directional drilling service that AnTech provides. It was also a great opportunity for our new drilling crew to get to know each other and meet our existing drilling team before the start of the job. AnTech has always been a global company and proud of the diversity within the company itself. It should then not be a surprise to know that the entire crew attending the training school came from 9 different nationalities and travelled to Exeter from 4 different continents. AnTech is proud of the new team members on board and everyone is looking forward to another successful year of operations around the world. If you would like any further information or would like to know more about Coiled Tubing Drilling please contact us or take a look at our website www.coiledtubingdrilling.com.
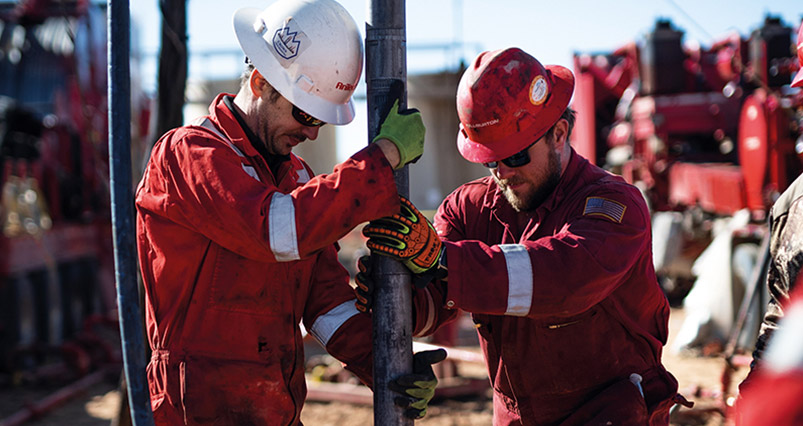
1567339200000
Collaborative Working Enables Valuable Real-Time CTD Decision Making
A recent project in the Texas Panhandle shows how collaborative working enables real time decision making. By Adam Miszewski, Global Operations Manager of AnTech Ltd. Underbalanced Coiled Tubing Drilling (UBCTD) offers operators a way to capture significant extra value out of known reserves. In fact, it has been comprehensively shown that, when applied correctly, the technology can deliver increased production rates at reduced cost when compared to traditional methods. It therefore makes maximising returns from declining fields a viable and attractive value proposition. However, in a traditional site set up, the technology is still held back by traditional ways of working. There are typically four principal service companies involved in a UBCTD campaign: the directional downhole tools provider, the coiled tubing service company, the underbalanced drilling fluids package and the operator. Each company uses its own data acquisition system (DAS). Typically, this means an incomplete data picture is available to any party at any given time. Consequently, there are delays in decision making on-site while data from the other parties are requested, collated and analysed. New proprietary technologies have come along that remove the delays inherent in these traditional ways of working. They enable real time decision making and take the productivity, operational and cost effectiveness of UBCTD together to the next level. As such, it opens up new opportunities for operators with declining fields. An example of such technology is RockSense that was demonstrated in a project led by AnTech in the Texas Panhandle. RockSense is AnTech’s proprietary synthetic porosity algorithm. RockSense has the ability to distinguish between difference formations by combining downhole and surface data in real time to give an at-bit qualitative measurement of porosity. It offers two considerable advantages over traditional geosteering techniques. Because wired telemetry has a high data rate, multiple measurements can be made for every foot drilled and operators can gain inch-level resolution. And because the data delivered are representative of conditions at the bit – not 20-25ft behind it – the driller can deliver an optimally placed wellbore, with more feet drilled in the target zone. To enable the use of technologies such as RockSense, a complete real time data picture is required. This means all parties involved in a project have to share their data in real time. For this to be achieved – and for operators to be able to take advantage of the enhanced capabilities technologies such as RockSense deliver – a different way of working that involves a very much more collaborative approach from the very earliest stages of a project needs to be embraced by the operator and the service companies. It’s a way of working that was embraced by an operator in the Texas Panhandle. Specialist contractors were utilised for each major component of the project and tightly integrated from the earliest stages using project management best practices. Its success showed the value of collaborative working in combination with UBCTD and digital technologies. Project background The project was a two well re-entry campaign in the Texas Panhandle. The wells were part of a wider campaign to revitalise a field that had been producing for many years. The overarching aim of the wider campaign was to intercept fractures and access untapped reserves to boost production. Underbalanced drilling was considered the best way to increase production because .it is known that preventing a formation from becoming overbalanced at any time can have a significant impact on production. Indeed, the expectation was that the production would remain high for a prolonged time due to the benefits of drilling underbalanced. UBCTD was chosen specifically because of the particular nature of the two wells. They were primarily gas producers, with condensate and water also being produced. UBCTD was seen as the best way to drill the reservoir underbalanced because it provided continuous stable underbalanced bottom hole pressure, as well as fast, safe and effective operation in two phase flow. In the early stages of the project, the operator decided to use new digital technologies for wellsite data acquisition, offsite support for data analysis and downhole sensors, by aggregating the data from all parties involved. By doing this, all parties would have a complete picture of what was happening on the wellsite and real time decision making would be improved. In order to enable this way of working, a great deal of time and effort was given to the planning phase prior to work starting on site – considerably more than would be traditionally expected. However, the operator recognised that such detailed planning and preparation was critical to the success of the project and encouraged the approach, creating a fully ingtegrated and effective working culture and operation. Figure 1: The interaction of service companies for the UBCTD campaign The role of aggregating the data was taken on by AnTech, the directional service provider. AnTech also provided pre-job engineering, pre-job project management, downhole equipment and data aggregation. Halliburton provided CT unit and pumps. ADA provided the flow back package. Blade Energy Partners provided pre-job engineering and wellsite supervision/ project management on site. (See Figure 1.) To enable the CT unit to run e-coil, AnTech provided the conversion kit to convert the rig to e-line (slip ring collector, collector bulkhead), work that was done well in advance of arriving at the wellsite. This collaborative way of working proved beneficial very early on in the project lifecycle. Early planning and collaboration helps address challenges The principal challenge needing to be addressed early on in the project was cost. The critical requirement was to stay in AFE, with a related aim of showing that UBCTD could be carried out cost effectively in the US and generate a significant ROI. Wellbore stability in the build section and water were two areas considered to be of particular concern.In terms of wellbore stability in the build section, the candidate wells had to be evaluated for stability in the overburden immediately above the pay zone. In terms of water, assessment was required because wells in the area had a history of watering out, so there was a risk of hitting water, which would significantly harm ROI. The large amount of time and effort put into the planning work was critical in ensuring that the wells were drilled as planned, that there were no surprises and challenges could be mitigated. To assess these challenges, a Hazard Identification study (HAZID) and Drill Well On Paper (DWOP) exercise were carried out before starting work with all the major service companies attending in person during the planning phase. This work helped to identify the major risks and mitigations required to complete the project successfully. The planning showed that only one candidate was able to be drilled underbalanced with an acceptable level of risk. All other wells had substantial amounts of shale interbedded with the limestone in the build section. There was therefore a high risk of shale instability. It was for this reason that the second well had an intermediate section drilled and cased by a conventional drilling rig. The planning also resulted in several other important outputs. It enabled the creation of a detailed set of written procedures that outlined exactly how the project was to be carried out. It also enabled contingency planning to deal with wellbore stability in the build section and water in the horizontal to be carried out. These contingencies included an expandable liner being kept on standby as a contingency for the wellbore stability and inflatable plugs being available in case of hitting water. The planning demonstrated that such contingencies were a sensible investment. To view the full article, please visit: MED OIL & GAS or contact us
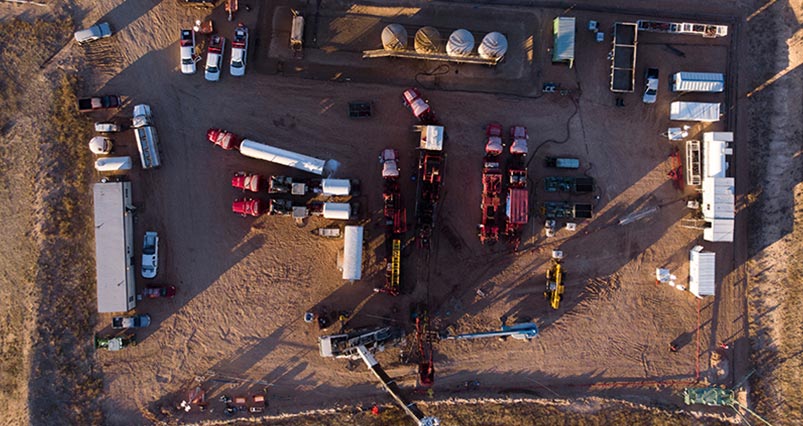
1560168000000
Success Drilling Wells In Texas Leads To Further Contracts Around The World For AnTech
At the end of last year AnTech, a specialist drilling provider, drilled two wells in the Texas Panhandle using advanced, patent pending, technology developed over the past two years at its Head Quarters in Devon. By Toni Miszewski, Managing Director of AnTech Ltd. The work was performed on a ranch in an environmentally sensitive area that also happened to be the site of a battlefield in the 1874 Red River war between American Indian tribes and the US Army. In the ground below the ranch, there is a natural gas field that has produced for decades, but over time production has declined and now more water is produced than gas. AnTech won a contract to re-drill wells based on its ability to drill with a completely enclosed drilling system and its ability to navigate precisely underground. Both of which reduce the environmental impact of the drilling process. The precise navigation is made possible by a new technique developed by AnTech called RockSense™ which sends a signal to the driller at surface, identifying what type of material is being drilled as the drill bit cuts into the rock. By comparing this information to geological maps, the measurement acts as a signpost to enable the driller to drill in the right place. Surprisingly, this capability, with such precision, has not existed previously. “Our engineers have worked hard to bring this technology to market, and it is testament to their skill and determination that we have managed to do it so quickly and effectively” said Toni Miszewski, Managing Director of AnTech. The success of this work has led onto further contracts which the company has recently signed with companies in Alaska and Australia. If you would like any further information or know more about Coiled Tubing Drilling then please contact us
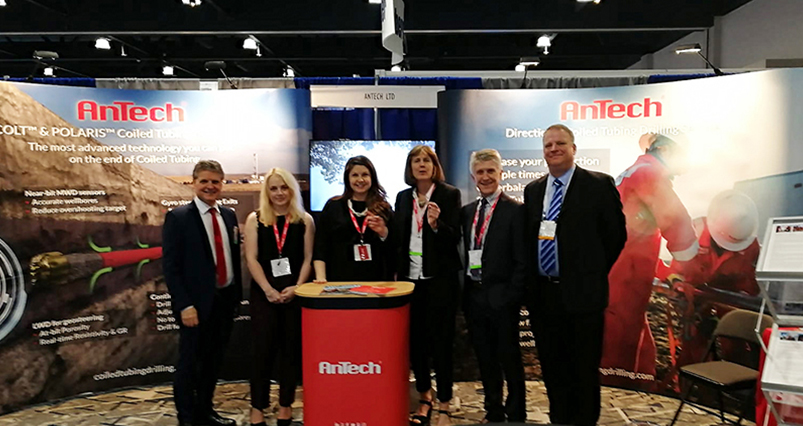
1554120000000
AnTech Attends SPE/ICoTA 2019: Well Intervention Conference & Exhibition
AnTech once again attended the annual SPE/ICoTA Well Intervention Conference & Exhibition held at The Woodlands Waterway Marriott Hotel and Convention Center in Houston, Texas, USA. It was hailed a huge success by all the AnTech team due to such a fantastic turnout of people within the industry attending the exhibition. On the booth, the AnTech team were busy discussing and answering questions about Directional Coiled Tubing Drilling throughout the duration of the show. As always, we had a great time attending the exhibition and being able to share our knowledge and technical expertise. The AnTech team would like to thank everyone who dropped by and had a chat with them and they’re already looking forward to attending next year’s SPE/ICoTA Exhibition at The Woodlands, Texas on 24th - 25th March 2020. If you would like any further information or would like to know more about Coiled Tubing Drilling please contact us
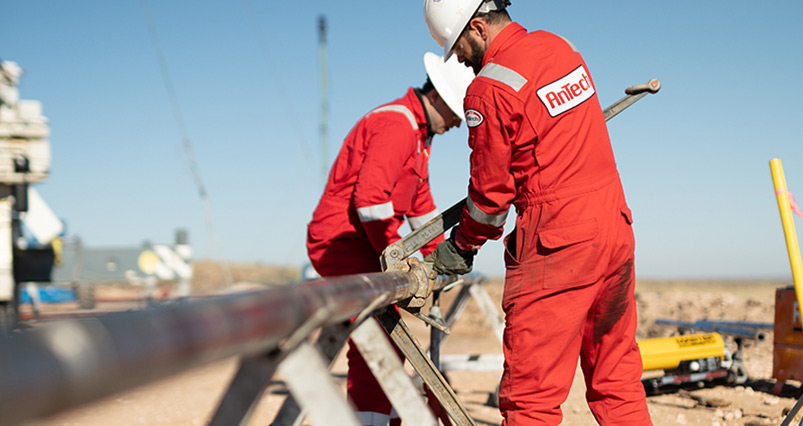
1551441600000
Data-Driven, Underbalanced CTD Improves Real-Time Decision-Making
A recent project in the Texas Panhandle shows the value digital technologies have to offer Underbalanced Coiled Tubing Drilling operations by Adam Miszewski, Global Operations Manager of AnTech Ltd. Underbalanced Coiled Tubing Drilling (UBCTD) offers operators a way to capture significant extra value out of known reserves and makes maximising returns from declining fields a viable proposition. Indeed, when applied correctly, such technologies have been shown to deliver increased production rates at reduced cost when compared to traditional methods. The technology is relatively new. Yet, as with all things these days, its newness has not stopped developments continuing apace. By combining the capabilities of UBCTD and the capabilities of digital technologies, another level of productivity, operational and cost effectiveness can be achieved. The capabilities of UBCTD can be seen in a recent project led by AnTech in the Texas Panhandle. Specialist contractors were utilised for each major component of the project and tightly integrated using project management best practices and digital technologies. As such, it can be said to represent the state-of-the-art not only in the region but across the industry as a whole. Project overview It is helpful to first provide an overview of the project and what it hoped to achieve. The project was a two well re-entry campaign in the Texas Panhandle and was part of a wider campaign to revitalise a field that had been producing for many years. The overarching aim of the campaign was to intercept fractures and access untapped reserves to boost production. Underbalanced drilling was seen as the best way to increase production from the field because it is known that preventing a formation from becoming overbalanced at any time can have a significant impact on subsequent production. Secondary reasons to drill the wells using UBCTD were stable underbalanced conditions, which is especially important when working with two-phase flow, and reservoir characterization while drilling allow accurate water shut off. In the case of the project under consideration here, the two wells were primarily gas producers, with condensate and water also being produced. UBCTD was seen as the best way to drill the reservoir underbalanced because it provided continuous stable underbalanced bottom hole pressure, as well as fast, safe and effective operation in two phase flow. Aggregating digital data was critical for project success In order to maximise the success of the first drilling campaign on the two wells, a great deal of time and effort was given to planning the operation. The operator was determined to put the right time and resources into the planning phase prior to execution; setting the whole operation up for success. In the early stages of the project, it was decided to take advantage of digital technologies in the form of wellsite data acquisition, offsite support for data analysis and downhole sensors by aggregating the data from all the parties involved. By doing this, all parties would be able to have a complete picture of what was happening on the wellsite and the speed of decision making could thus be improved. There was another reason for aggregating the data in real time. This was because RockSense, AnTech’s proprietary synthetic porosity algorithm, was to be used on the project and this required a complete real time data picture. RockSense has the ability to distinguish between different formations by combining downhole and surface data in real time to give an at-bit measurement of porosity. It offers two considerable advantages over traditional geosteering techniques. First, because wired telemetry has a high data rate, multiple measurements can be made for every foot drilled and operators can gain inch-level resolution. Second, because the data delivered are representative of conditions at the bit – not 20-25ft behind it – the driller can deliver an optimally placed wellbore, with more feet drilled in the target zone. However, for data aggregation to be achieved in real time, a very much more collaborative approach from the very earliest stages of the project was needed. It is perhaps worthwhile briefly touching on why this was the case. There are typically four principal parties in a UBCTD campaign: the directional downhole tools provider, the coiled tubing service company, the underbalanced drilling fluids package and the operator. Each service company uses their own data acquisition system (DAS). This means an incomplete picture is available to any party at any given time and there are delays in decision making while data from the other parties is requested, collated and analysed. Figure 1: The interaction of service companies for the UBCTD campaign The role of aggregating the data was taken on by AnTech, the directional service provider. AnTech also provided pre-job engineering, pre-job project management, downhole equipment and data aggregation. Halliburton provided CT unit and pumps, ADA provided the fluids separation package and Blade Energy Partners provided pre-job engineering, Wellsite Supervision/ Project management on-site. (See Figure 1.) To enable the CT unit to run e-coil, AnTech provided the conversion kit to convert the rig to e-line (slip ring collector, collector bulkhead), work that was done well in advance of arriving at the wellsite. To view the full article, please visit: World Oil or contact us
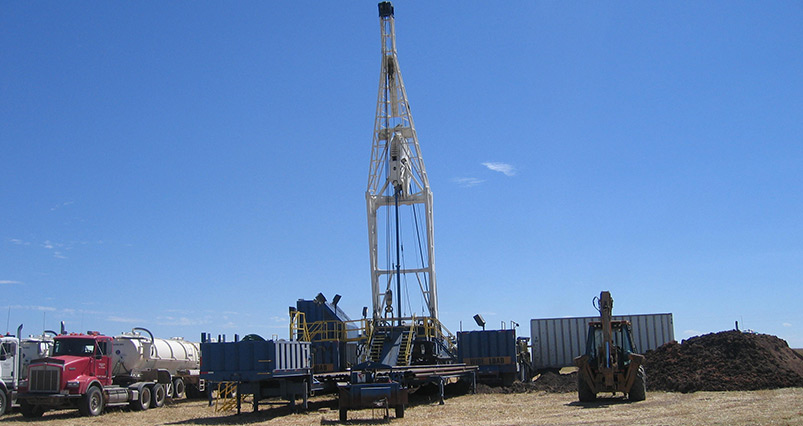
1542024000000
Med Oil & Gas Winter Magazine 2018: AnTech's Polaris Technology
Coiled Tubing Drilling: Directional and Horizontal Drilling with Larger Hole Sizes by Toni Miszewski, Managing Director of AnTech Ltd. Coiled Tubing Drilling (CTD) is a well-documented technique that has, to date, been used with great success for grassroots vertical wells, where wells have been drilled and cased in a day, along with directional through tubing re-entry work, where it is used to further exploit existing wells, such as the operations carried out in Alaska and the Kingdom of Saudi Arabia. However, in these directional operations the hole sizes drilled with coiled tubing are relatively small (up to 4.5”). There is increasing demand from markets such as shale gas, coal bed methane and underground coal gasification (UCG) for larger hole sizes, but until now there has not been an economically viable option for drilling directional wells with coiled tubing in the 6.25” to 8.5” range. However, the production of a BHA in this size has been made cost-effective through the use of an innovative solid state gyro system for directional measurement at all inclinations. The use of a gyro system whilst drilling, instead of a magnetic steering tool, removes the need for non-magnetic materials and allows the tool to be made much shorter. To demonstrate the capability of this tool, a 5-well drilling program was completed in Kansas, USA between November 2011 and February 2012, using a combination of a hybrid drilling rig and a 5.0” Bottom Hole Assembly (BHA), with a Rotating Orienter. Various directional and horizontal well profiles were drilled with hole sizes from 6.25” to 8.5”. The aim of the program was to demonstrate this new technology with the intention of providing a more economic drilling option and to show that the combination of a hybrid rig and this new BHA can be used to efficiently drill and case directional and horizontal wells with hole sizes from 6.25” to 8.5”. Furthermore, an additional goal of the program was to carry out some initial vibrational analysis into the forces experienced while drilling and investigate how this could inform future equipment testing and operations. To view the rest of this article and for more information please contact us
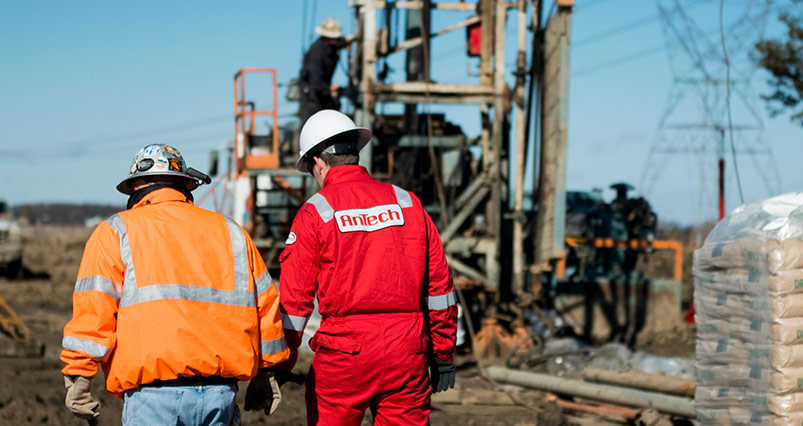
1540987200000
Project Demonstrates Directional Coiled Tubing Drilling's Benefits
Toni Miszewski, Managing Director and Adam Miszewski, Global Operations Manager of AnTech, show how project demonstrates DCTD's benefits to The American Oil & Gas Reporter. PITTSBURGH, PA.–An underbalanced directional coiled tubing drilling (DCTD) project in the Appalachian Basin demonstrates the potential for using CTD technology to realize the economic potential of marginal oil wells in shallow conventional plays. The objective was to drill a lateral sidetrack to access target zones identified adjacent to a recently drilled vertical dry hole. The target thickness was 15 feet, making accurate depth control critical. It also was considered essential to drill the entire reservoir underbalanced using nitrified fluids to minimize formation damage. The offset wells surrounding the sidetrack location produce 10-100 barrels of oil a day with up to 80 percent water cuts. Given the typical low daily production rates in the field, the challenge was to deliver a productive horizontal sidetrack in a cost-efficient manner. There are two ways to alter the economics of a well: reduce costs or increase production. For an individual marginal well with a low production, there comes a point below which costs cannot be reduced sufficiently to make a material difference to the economics. Therefore, the focus of this project was on applying a specialized DCTD bottom-hole assembly and engineering software package as the enabling technologies to increase production while containing the drilling costs to make the extra production more profitable. Drilling efficiency is often measured in terms of cost per foot, and while this is an important measure, the target of this DCTD project was to define drilling efficiency in terms of cost per production rate. This measure takes the initial production into account, and in the process, ties together the ability of the driller to make hole in the direction required with the ability of the geologist and reservoir engineer to select a productive part of the formation. Recognizing that each stage of well construction can affect another, a multidisciplinary approach was adopted to include inputs from geology, geophysics, reservoir engineering, drilling and completions engineering. Local experience with offset wells also was an important input, allowing for the fact that all offsets were vertical wells drilled with air or in an overbalanced condition. The overall objective was to increase cash flow from the well by accessing more of the reservoir using a horizontal wellbore. A horizontal trajectory also allows for natural fractures to be easily intercepted for increased production. Ultimately, successful horizontal wells could reduce the total number of wells that need to be drilled to fully exploit the reservoir. Potentially, one horizontal well with a second lateral branch could replace four wells with an associated cost reduction. Drilling horizontally in an underbalanced condition using nitrified fluids to avoid formation damage required more sophisticated equipment than what is traditionally used on shallow low-volume wells, but at the same time, the extra capability was required to realize the reservoir’s potential. The field is sufficiently depleted for the wells not to produce to surface and the reservoir has low permeability, making it susceptible to damage from drilling fines being forced into the formation. Underbalanced drilling also typically increases the rate of penetration to shorten the required drilling time. Planning Process As noted, the DCTD project was conducted in a field with numerous vertical offset wells and a good understanding of the local geology. Vertical well depths in the field typically do not exceed 2,500 feet. Four vertical wells had been drilled by Chuck Henry Energy LLC and its partner, Hocking Hills Energy, in the immediate vicinity in the previous year, three of which were on production yielding rates of 10-25 bbl/d with varying levels of associated water. Although the fourth well had shown production promise based on electric logs, it turned out to be dry. Consequently, a planned 4 ½-inch production casing string was not run in the well and it had not been completed. Any of the wells could have been chosen as a candidate for DCTD, but after analyzing the different options, the uncased well was chosen because a value analysis indicated that it had the shortest payback period if it could produce at a similar rate to neighboring wells. The sidetrack was planned to access a different volume of the reservoir than the vertical bore hole, and the fact that the vertical well had not been completed had the added benefit of avoiding losing existing production to drill the sidetrack. To view the rest of this article and for any information or enquiries please contact us
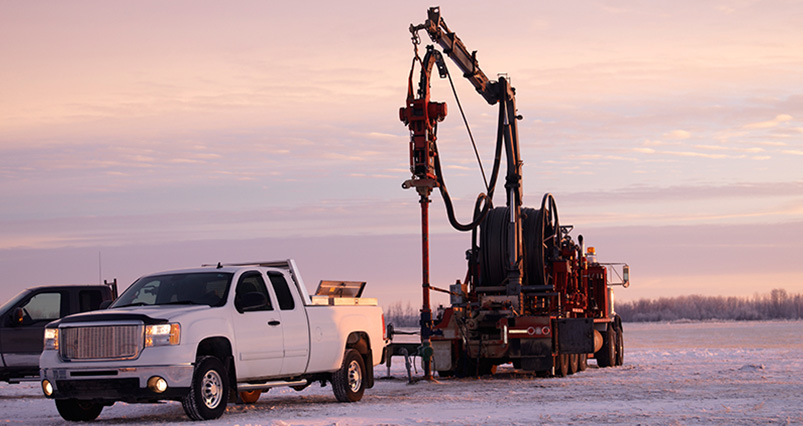
1538136000000
Reaching A Turning Point: Underbalanced Coiled Tubing Drilling
Adam Miszewski, Global Operations Manager of AnTech discusses underbalanced coiled tubing drilling seeing wider implementation in today's changing oil field. Underbalanced coiled tubing (CT) drilling (UBCTD) has continually advanced since the first trials in the 1990s but remains a relatively niche drilling technology. Most of the wells drilled using UBCTD in the past decade have been in Saudi Arabia and Alaska. Like horizontal drilling and unconventional resources before it, UBCTD has been extensively trialled and optimized on fields around the world, and it would seem that now—with projects set to start in Oman, Abu Dhabi, Indonesia, New Zealand, and the US in the next year—we have reached a turning point for UBCTD implementation. Drilling underbalanced on CT requires three components: Coiled tubingAn underbalanced fluids systemA directional bottomhole assembly (BHA) The way these technologies are used is similar to the way they are used in conventional drilling, but there are some differences. The CT is usually 2⅜-in. or larger and must have an e-line installed. It is not required to use a CT unit specifically designed for UBCTD; nearly all CT units can be converted for the purpose. UBCTD BHAs run on e-line so that communication can be maintained when drilling with two-phase fluids—for example, water and nitrogen. An advantage of this is that downhole readings are communicated to surface in near real time, which provides the operator with a greater opportunity to utilize the downhole measurements. The concept behind directional drilling a well on CT is very similar to conventional drilling with mud motors. The motors have a bent housing so that the bit is pointed in a certain direction, called the toolface. The orientation of the toolface decides the direction of the well. This can be adjusted to change course or it can be rotated continuously to drill straight and hold sections. As CT cannot be rotated, all toolface orientation must be carried out downhole using an orienter module. This module is controlled electrically from surface, and it is key that the orienter can continuously rotate, when required, to drill the straight-hole sections. The high-speed communication to surface means that directional drilling on CT is very fast paced, with small toolface changes being possible and real-time responses communicated from the tool. The fluids package for underbalanced drilling projects needs to be able to separate out the drilling fluids and produced fluid from the well; as the well is underbalanced, produced oil, gas, and water will flow to the surface. A conventional underbalanced drilling fluids package has to deal with rotating pipe and therefore requires a significant amount of maintenance, making the fluids package a weak point in the system. However, for UBCTD operations the package can be connected up without having to deal with any rotating components or connections. This guarantees a stable downhole pressure, preventing any overbalance from damaging the formation, while also minimizing failure points in the system. UBCTD is not a new concept but technology advancements over the past few years have created opportunities for operators to take advantage of its benefits without having to foot the cost of a new technology. CT is now available in larger sizes that provide greater flow rates and lateral reach. Downhole tools are now much smarter with a full measurement-while-drilling suite, including downhole weight-on-bit, gamma, and pressure-while-drilling. On-surface data can be combined from all the equipment packages and displayed quickly so that real-time decisions can be made. There have been major technological advances in other parts of the oil field, so what could be attracting operators to start utilizing UBCTD as the oil and gas industry is still reeling from the worst industry downturn in decades? The advantages of UBCTD can be focused into two categories—production advantages and operational advantages. Depending on the project, an operator is likely to be focusing on one of these categories, with the other advantage coming as an additional benefit. Production advantages are as follows: Maximizing production by avoiding formation damageAccessing bypassed reservoirsIncreasing well data from the underbalance results Operational advantages include: A smaller footprintSpeed of operation, including high rate of penetration when drillingAn environmentally friendly system Note that these are not exhaustive lists, and operators will have unique considerations that will affect their decision to use UBCTD. However, no technology is without limits, and UBCTD has its own limitations. The technology is targeted at reservoir drilling and is not suitable for tophole or intermediate sections unless on very shallow, simple wells. The other major limitation is in the horizontal lateral length. Horizontal sections up to 5,000 ft can be achieved with the right well profile but extended lengths present a significant challenge. In addition, personnel training and experience and equipment availability are limits to quickly scaling the use of UBCTD. Technology has revolutionized every industry in recent years and the oil industry is no different. UBCTD technology has now advanced to the point where it can compete commercially and make some forward-thinking operators a good return. The next few years will show if it has the ability to revolutionize the industry or if it will stay as a niche technology. To view this article online please visit: SPE For further information or enquiries please contact us
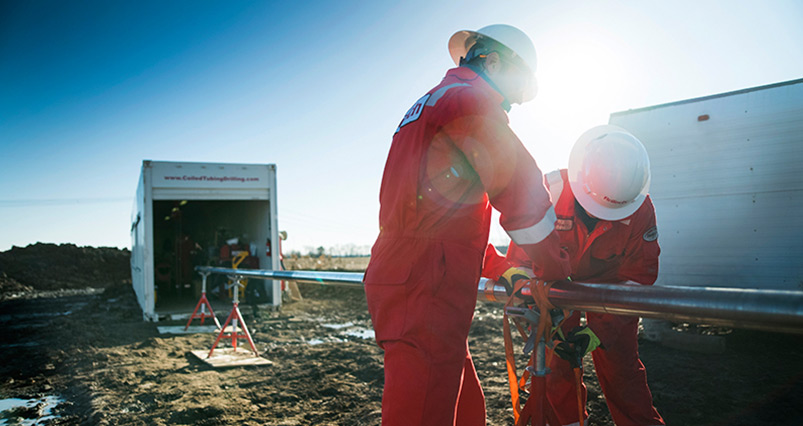
1537358400000
Interview With Pipeline On Coiled Tubing Drilling
Toni Miszewski, Managing Director of AnTech talks about the benefits of Coiled Tubing Drilling when it comes to productivity, safety and environment with Pipeline Magazine's Nadia Saleem. 1. What's your latest technology in drilling? AnTech offers a directional drilling service using coiled tubing, Coiled Tubing Drilling. Our service is based on the latest generation of bottom hole assemblies which have been designed to take advantage of the developments in experience and technique gained over recent years. We have developed a range of equipment that is easy to deploy, reliably survives the rigours of underbalanced drilling and is capable of working seamlessly with the coiled tubing unit and fluid flowback equipment to provide a fully integrated technical solution. 2. How does AnTech's coiled tubing drilling bring production and cost efficiency? The value proposition of Coiled Tubing Drilling is very straight forward. A lot of wells have more to give in terms of production and by re-entering the wells and drilling horizontally and underbalanced it is possible to significantly increase that production. Coiled Tubing Drilling provides a way to do it economically. Every well starts to decline shortly after it is put on production. Additionally, many older wells were drilled vertically with only the technology that was available at the time. Almost exclusively wells were drilled with a mud column providing an overbalanced pressure. There are two proven methods of increasing production from wells. One is to drill horizontal wells to provide more reservoir contact and the other is to drill underbalanced so that the well is flowing at the same time as the well is being drilled. This prevents damage to the reservoir. Every field is different but a combination of these two techniques has provided increases in production in excess of 5 times and payback times that can be measured in weeks. Where coiled tubing comes in to this is that it is a technique that is specifically designed for drilling this type of well. In fact, if you were starting to design a method of drilling from scratch, you would end up with a coiled tubing drilling system with a hybrid coiled tubing rig as the best way of meeting safety, environmental and productivity requirements. 3. How involved are you with the digitalisation transformation that the oil and gas industry is increasingly moving towards? Coiled Tubing Drilling runs on an electric wireline inside the coiled tubing. This gives us the capability to transmit a lot of data to surface. When drilling, the system generates at least 3 orders of magnitude more data than conventional jointed pipe drilling. This data contains a mass of information that has previously either been ignored or more likely, did not have enough detail to me able to make meaningful deductions. We process this information to provide more insight to the drilling process than was previously possible. This year we have launched RockSense™ our at-bit geosteering service for Coiled Tubing Drilling. Using proprietary algorithms and combining uphole and downhole data from sensors in our bottom hole assemblies, it gives us the capability to detect changes in porosity at the bit with up to a 6-inch resolution. This has tremendous value for the directional driller who is steering the tool and ultimately to the well owner because it can result in faster drilling operations and more accurately placed wellbores with more hole drilled in the target zone. 4. What's your business outlook and targets for the near to medium term? Last year was a particularly active year for Coiled Tubing Drilling tenders around the world with, at one time, six separate tenders being active. Four of these were in the MENA region showing that operators in the region see the economic benefit of Coiled Tubing Drilling. Over the past decade Aramco has shown how to successfully use Coiled Tubing Drilling to increase production and other operators are keen to emulate this success. Interestingly, three of the six tenders were for offshore projects. The two long term projects in Alaska and Saudi Arabia are both land projects. Offshore projects are usually more of a logistical challenge than land projects due to the lifting and space constraints. At the same time, drilling work with coiled tubing can be much more cost effective than the alternative which would mean bringing in a jack-up rig. We are seeing other offshore projects where operators are grappling with the problem of how to extend the life of expensive offshore installations whilst at the same time controlling costs to make sure that any interventions are economically viable. With the increasing price of oil, we expect the interest in Coiled Tubing Drilling to increase as operators look to take advantage of higher prices. In the last few years, operators were looking to Coiled Tubing Drilling as a way to drill economically with oil prices as low as $40/bbl. Now, as the market picks up, there is a question of equipment availability. In some regions it is now difficult and expensive to mobilise jointed pipe rigs. That is where the mobility of Coil Tubing Drilling has an advantage. 5. What are your main markets and how important is the Middle East region? Coiled Tubing Drilling is applicable to any region where there are fields that are experiencing a production decline. As 80% of the world’s production comes from declining fields that means that there is a worldwide opportunity for Coiled Tubing Drilling. In a practical sense though, we have to focus on particular markets. For us, that means the Middle East and the US. Aramco invested in AnTech to support the introduction of the latest technology into the Kingdom of Saudi Arabia and we are already set up to support work there in the near future. In the US, where recent focus has been on unconventional wells, with the increase in the oil price, we are expecting an increase in re-entry work for conventional oil and gas wells. To view the magazine article please visit: Pipeline oil and gas news For further information or enquiries please contact us
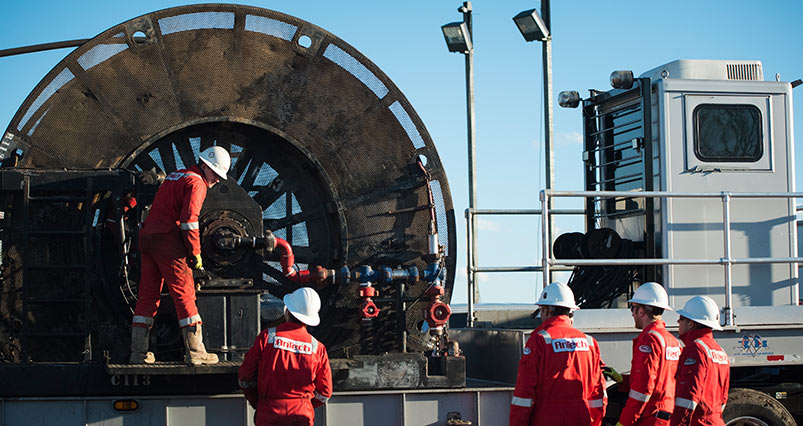
1536753600000
Med Oil & Gas Summer/Autumn Magazine 2018: AnTech's Rocksense Technology
The precise depth at which a target formation will be penetrated by the bit is never known with certainty until the well is actually drilled. Yet maximising recoverable reserves depends on optimal wellbore placement, which in turn depends on reacting to the newly confirmed knowledge of a formation boundary’s whereabouts the moment it is discovered. A new technology, RockSense, provides at-bit bed boundary identification while Coiled Tubing Drilling and gives engineers and directional drillers as new tool in the Geosteering toolkit. Richard Stevens, Coiled Tubing Applications Engineer at AnTech Ltd. Mechanical Specific Energy was first proposed by Teale in 1965. MSE provides a way to characterise the energy required to drill a length of hole in a formation. It follows that, as the drill-ability of the formation changes, so does the energy required to drill it. It turns out that a plot of MSE vs Depth for a section of hole is a very good proxy for porosity, and the fact that it is an at-bit measurement makes it an extremely useful tool to have when navigating vertically limited formations. The calculation of MSE requires real time measurement of Weight-on-Bit (WOB) and Torque. Historically, downhole Weight-on-Bit and Torque were derived from surface measurements, with corrections applied for the effects of buoyancy and friction. The error inherent in these empirical corrections was usually greater than the signal in the subtle changes in MSE due to differing formation characteristics. In other words, the signal from the formation was lost in the noise of the corrections. Latterly, technology advances have permitted downhole measurement of WOB and Torque, but mud pulse bandwidth limitations have imposed severe constraints on the definition that has been possible. The latest generation of Coiled Tubing Drilling BHAs, featuring integrated downhole sensors and high speed wired telemetry, provide a technology platform that finally makes high definition MSE measurements possible, opening a new window on the downhole environment as drilling progresses. The technology has sound, intuitive footings. Picture yourself a passenger in a moving car. Even with your eyes closed, you know the type of road you’re travelling on (freeway, city street, dirt road) by the road noise you can hear. Anyone who has ever drilled a hole in a masonry wall to hang a picture, or fit shelves will have experienced the principle at first hand. Without even thinking about it, the person holding the drill is aware when he is drilling the plaster, when he is drilling brickwork and when / if he hits a void in the brickwork. Consider now a motor turning a drill bit which drills a hole in a sample of rock. We can measure the power input to the motor as the hole is drilled to gain an understanding of the type of rock we’re drilling. If it was an electric motor we would simply measure the voltage applied and the current flowing during drilling and multiply them to get the instantaneous power. For a positive displacement mud motor it’s slightly more complicated, but it can be done. If differential pressure and flow rate can be measured then, given knowledge of principal operating constants for the motor, an expression for power in terms of pressure and flow rate can be written. If we were then to integrate this power as the hole progresses we would have a value of Energy expended per foot of hole drilled and would therefore have a relative indicator of the changes in formation being drilled. In this fashion, by continually monitoring torque, WOB, pressure and ROP, AnTech’s RockSense provides information about the formation being drilled, as drilling proceeds. The high data rate offered by wired telemetry, permits multiple measurements to be made per foot of hole drilled, yielding inch level resolution in the processed signal. To view the rest of this article and for more information please contact us
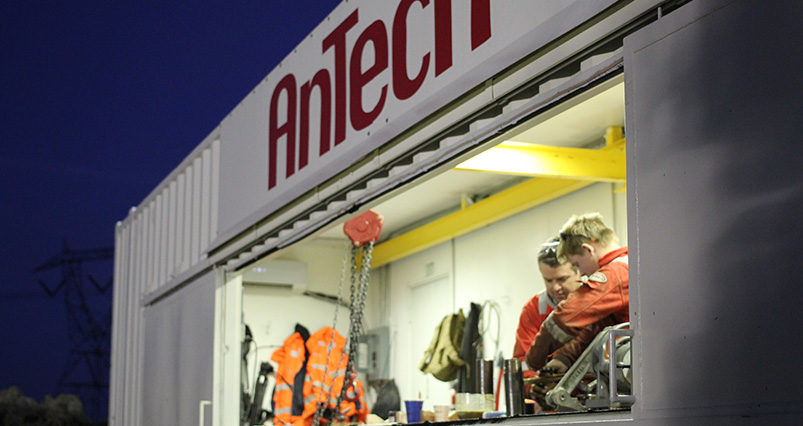
1535716800000
Geosteering CTD Using The Drill Bit As A Sensor
The precise depth at which a target formation will be penetrated by the bit is never known with certainty until the well is actually drilled. Yet, maximising recoverable reserves depends on optimal wellbore placement. This, in turn, depends on reacting instantaneously to the newly confirmed location of a formation’s boundary. A new technology, RockSense, provides at-bit bed boundary identification while Coiled Tubing Drilling gives engineers and directional drillers a new tool in the Geosteering toolkit. By Richard Stevens, Coiled Tubing Applications Engineer at AnTech. Setting the scene Mechanical Specific Energy, first proposed by Teale* in 1965, provides a way to characterise the energy required to drill a length of hole in a formation. It follows that, as the drill-ability of the formation changes, so does the energy required to drill it. Therefore, a plot of MSE vs Depth for a section of hole is a very good proxy for porosity. Additionally, as an at-bit measurement, it is an extremely useful tool for navigating vertically limited formations. Historically, downhole Weight-on-Bit and Torque were derived from surface measurements, with corrections applied for the effects of buoyancy and friction. The error, inherent in these empirical corrections, was usually greater than the signal in the subtle changes in MSE due to differing formation characteristics. The latest generation of Coiled Tubing Drilling BHAs, featuring integrated downhole sensors and high speed wired telemetry, provide a technology platform that now makes high definition MSE measurements possible, opening a new window on the downhole environment as drilling progresses. The technology has sound, intuitive footings. Picture yourself a passenger in a moving car. Even with your eyes closed, you know the type of road you’re travelling on (freeway, city street, dirt road) by the road noise you can hear. Anyone who has ever drilled a hole in a masonry wall to hang a picture, or fit shelves, will have experienced the principle at first hand. Without even thinking about it, the person holding the drill is aware when he is drilling the plaster, when he is drilling brickwork and when/if he hits a void in the brickwork. Consider now a motor turning a drill bit which drills a hole in a sample of rock. We can measure the power input to the motor as the hole is drilled to gain an understanding of the type of rock we’re drilling. If it was an electric motor, we would simply measure the voltage applied and the current flowing during drilling and multiply them to get the instantaneous power. For a positive displacement mud motor, it’s slightly more complicated, but it can be done. If differential pressure and flow rate can be measured, then, given knowledge of principal operating constants for the motor, an expression for power in terms of pressure and flow rate can be written. If we were then to integrate this power as the hole progresses, we would have a value of energy expended per foot of hole drilled and would therefore have a relative indicator of the changes in formation being drilled. In this fashion, by continually monitoring torque, WOB, pressure and ROP, AnTech’s RockSense provides information about the formation being drilled, as drilling proceeds. The high data rate offered by wired telemetry, permits multiple measurements to be made per foot of hole drilled, yielding inch level resolution in the processed signal. Highlighting the need for a new Geosteering methodFigure 1a. Planned side-track well based on linear interpolation of formation tops Figure 1b. Actual side-track well misses formation due to a non-linear formation top depth between the vertical wells Look at Figures 1a and 1b. Based on formation tops observed in previously drilled vertical wells, a horizontal side-track is planned based on a casing exit depth, a build rate that will land the lateral the required distance below the top of the reservoir and a target inclination which will track the top of the reservoir. A modern directional Coiled Tubing Drilling BHA will be able to feed directional information (inclination and azimuth) to the surface as drilling proceeds which can be combined with bit depth to provide an accurate estimation of the borehole’s position in 3D space. But, if the top of the reservoir formation is not flat – more like that in figure 1b, then navigation by dead reckoning alone will land you in the seal, not the reservoir. The solution to this problem is the well-established art of Geosteering. Geosteering is the practice of directing the borehole in response to observed characteristics of the formation. Sensors, such as gamma, resistivity, porosity are available to measure distinguishing characteristics of the formation. Although these sensors are mature, with good reliability and consistent performance, a significant feature which affects their use in Geosteering is the position of the sensor along the BHA. The BHA is constrained by its nature to be a long, thin tube. Maybe 3 inches in diameter and many tens of feet long. At the bottom of the BHA is the bit, immediately above this, by necessity, is the mud motor, occupying 10-15 ft of BHA length, and the directional sensor package is normally located immediately above the BHA. This means that sensors sensitive to identifying characteristics of the formation are constrained to be at least 20 – 25 ft behind the bit. The significance of this in Geosteering terms is illustrated in figures 2a and 2b. This means that a change in formation characteristic won’t be visible to the sensor until a further 20-25 ft of hole has been drilled in the formation. As figure 2 illustrates, this implies a corresponding delay in informed steering decisions, with the consequence that the formation of interest may be exited before a steering correction can be made. If the additional vertical depth traversed during the delayed steering correction happens to be water bearing, the negative impact on lifetime productivity of the well can be significant. Even if there is no productivity impact, time spent drilling unproductive formation will impact the project’s bottom line. As figure 2b illustrates, the ability to make a steering decision at the time that the bit penetrates the formation results in a much better chance of staying within the target formation. Geosteering can also be informed by the analysis of cuttings. However, the time taken to circulate cuttings to surface, capture them and prepare them for analysis means a delay, similar to that described above. . Meanwhile, the bit continues to turn, meaning that, once again, the formation of interest is substantially penetrated before positive confirmation is received, reducing the TVD available to successfully complete a steering action. Dispersion of cuttings in the annulus (different sizes and densities travel at different speeds) can also adversely affect depth resolution. Exploring the solution in practice Although RockSense is available as a real time service to inform navigation decisions while a well is being drilled, the system works just as well with historical data sets. Two data sets have been chosen for analysis, based on the availability of conventional logs from adjacent wellbores for corroboration. The first data set is from a Coiled Tubing Drilled side-track of a well in North America. The well was in a densely drilled locality and open hole logs for nearby vertical wells were made available. No horizontal wells had been drilled in the area previously and the objective was to production through increasing reservoir contact. The operator used 3D seismic to evaluate the formations and identified a subsurface ridge that could be acting as a trap. The well path was planned to pass approximately 15 ft below the formation top and track the formation by holding inclination. The oil/water contact was believed to be 40 ft below the formation top and, if it was entered, would significantly impact the well economics. Gamma ray sensors were used for depth correlation because relying on seismic depth alone would not provide the depth accuracy required. The hole section was drilled using single phase fluid in the build section. Running the RockSense software on the data gathered during this job revealed compelling similarity in the shape of the density log for nearby wells and the RockSense trace when plotting porosity against TVD, as can be seen in Figure 3. Figure 3. Compelling similarity between the shape of the density log for nearby wells and the RockSense log when plotting both quantities against TVD (Note that the RockSense scale is offset in this view) The second data set involves Underbalanced Coiled Tubing Drilling in a shale gas well, also in the United States, which is illustrated in Figure 4. In this instance, a 4¾” lateral was drilled using Underbalanced Coiled Tubing Drilling with a mixture of up to 40% nitrogen to minimise formation damage. It was intended that the wellbore should stay within an identified formation layer. Post processing the historical data using the RockSense software clearly identifies a substantial footage drilled below the target formation. Were that lateral to be drilled today, with real time RockSense on screen, a more reactive steering strategy could have been followed. In this more reactive strategy, RockSense would be used to identify crossing the formation top, at which time the trajectory would be adjusted to follow the formation dip, with RockSense being monitored as a guard against exiting the formation. Figure 4. Applying RockSense historically reveals its sensitivity to boundary crossings In summary, RockSense delivers an at-bit bed boundary identification service of a type not seen before. The service is delivered in real time, as the hole is drilled. It is made possible by the low latency, high rate transmission of data from high fidelity downhole sensors. The parameters measured are representative of conditions at the bit – not 25 feet behind the bit, giving the driller a 25 ft head start in making his steering decisions. This potentially disruptive service means he can deliver an optimally placed wellbore, with more feet drilled in the target zone, resulting in improved lifetime productivity, higher initial production and substantially improved project economics. *MSE. Teale, R.: “The Concept of Specific Energy in Rock Drilling”, Intl. J. Rock Mech. Mining Sci. (1965) 2, 57-73. If you would like more information please contact us
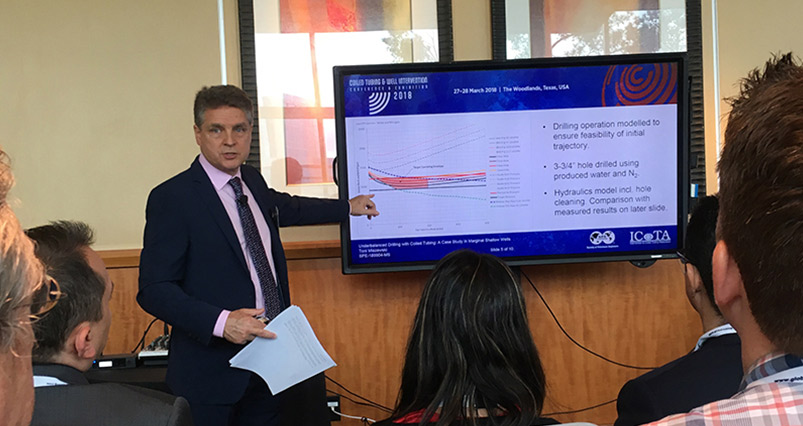
1530273600000
On The Move: AnTech's Latest Fixtures & Events
The first half of 2018 has been busy with AnTech travelling extensively to promote its Directional Coiled Tubing Drilling technology. Towards the end of March, Managing Director, Toni Miszewski presented at the ICoTA conference in Texas. Based on a case study in Marginal Shallow Wells, Toni discussed the merits of Underbalanced Drilling with Coiled Tubing. A paper discussing this Case Study is available for purchase from the Society of Petroleum Engineers (SPE). It discusses the successful re-entry of a dry hole, which was side-tracked to create a productive well. In May, Toni travelled again, this time to Houston, to present At-bit Geosteering for Coiled Tubing Drilling. This technology allows engineers and directional drillers to instantaneously ascertain the formation boundaries as drilling progresses. This maximises recoverable reserves by ensuring optimal wellbore placement. In May, Adam Miszewski, AnTech’s Global Operations Manager, travelled to Manama, Bahrain to present AnTech’s technology RockSense at the Society of Petroleum Engineer’s Workshop. Most recently, in June, Adam again presented on RockSense, this time discussing Slim Hole Drilling including TTRD, coiled tubing drilling and advances in expandable and multilateral technology at the European Drilling Engineering Association meeting hosted by Premier Oil in Aberdeen, Scotland. We have thoroughly enjoyed these fantastic opportunities to share our knowledge and to learn from our peers in the industry and we look forward to more in the future. For further information or enquiries please contact us
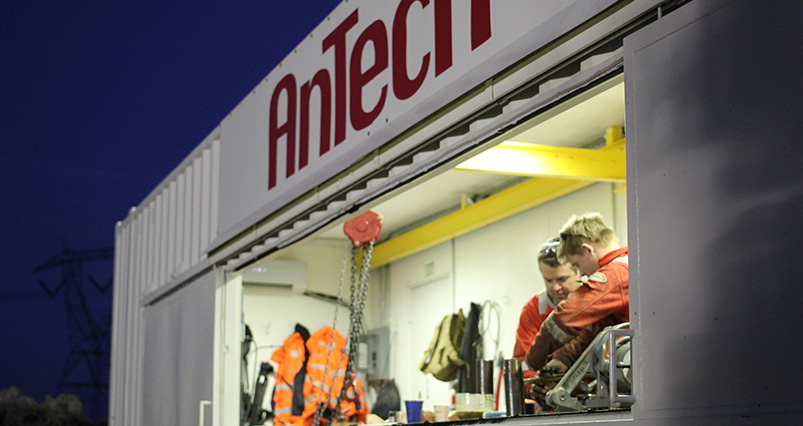
1524744000000
Geosteering CTD Using The Drill Bit As A Sensor
Placing the wellbore trajectory in the correct formation is crucial to project success. Existing geosteering techniques provide some of the necessary accuracy but can involve drilling a certain amount of unproductive formation. However, a new technology has the ability to give engineers the information they need to geosteer more accurately in real time at a reduced cost. By Richard Stevens, Coiled Tubing Applications Engineer at AnTech In today’s oil price environment it’s more important than ever to place the wellbore in the most productive formation. The depth of the formation on a wellpath is never known with absolute certainty until the well is actually drilled. There are two ways in which this problem can be minimised. The first is to rely on seismic data and as-drilled data combined with a certain amount of linear interpolation and assumptions on the properties of the rock. The second is to use geosteering. The latter is more accurate than the former, but neither offers an optimal solution. Let’s remind ourselves why. Linear interpolation and its limitations Figure 1a and 1b show the problems that can occur when relying on linear interpolation. Knowing the depth and dip of the top of the reservoir and having knowledge of the performance of the directional drilling equipment proposed for the job, it is perfectly possible to plan a wellbore trajectory based on a casing exit depth and a build rate that will land the lateral the required distance below the top of the reservoir combined with a target inclination which will track the top of the reservoir. A modern directional (CT) drilling BHA will be able to feed positional information (inclination and azimuth) to the surface as drilling proceeds. This information can be combined with bit depth to provide an accurate estimation of the borehole’s position in 3D space. Seismic data and offset wells provide valuable information when planning a well but there are inherent uncertainties in TVD based on the parameters and assessments made by the geophysicist. This is corrected to a certain extent by combining seismic interpretations with formation tops taken as-drilled on nearby wells. However, this still leaves an amount of uncertainty in the exact formation top location and a further problem arises when the formation is too thin for the trajectory to be planned below the lower uncertainty limit of the formation top or if the formation comes in at a different depth to that predicted by the subsurface team. If the seal drops below this line, as pictured in figure 1b, the ‘dead reckoning’ navigated well risks being drilled entirely in the seal. The issue is not only a problem at the top of the reservoir but also at the bottom. If the formation below is unproductive and comes in shallower than the expected depth, the well profile could pass entirely through the unproductive deeper formation. What the driller needs, to be able to avoid this non-profitable outcome, is information about what he is drilling through, in addition to pure positional information. This is what geosteering provides. Geosteering options and challenges In geosteering, properties of the formation being drilled are measured and used to modify the wellbore plan as it proceeds. It offers a considerable advance on simple interpolation, but there are still drawbacks. We’ll look at these briefly and then consider a new development – RockSense – that overcomes them and offers a greater degree of drilling accuracy at a reduced cost compared to LWD systems. Observing cuttings at surface The most basic (though by no means primitive) geosteering technique is to directly observe cuttings at surface. Cuttings are collected as they pass over the shaker, and subjected to optical, chemical, spectrographic or electronic analysis. There is a delay inherent in this process because of the time taken for cuttings to travel from the bit to the surface and the time taken to physically prepare and analyse the sample once it has arrived at surface. In deeper wells this time can be up to an hour. During this time, the wellbore may have progressed 30 ft or more, something that presents complications should the cuttings data not match the prognosis. Another significant drawback to this method is that the resolution is low. By the nature of the cuttings transport, the cuttings are dispersed on their journey to the surface which can make it hard to tell exactly when the bit passed through the formation top. Adding sensors to the CTD BHA The CTD BHA can be equipped with sensors that measure parameters which characterise the formations being drilled. They may provide information more quickly than observing cuttings, but they’re also add significant cost to the BHA. Modern Logging While Drilling (LWD) tools can accurately measure formation gamma signature, resistivity, density and porosity. The above tool-mounted sensors are mature, reliable and offer a high degree of discrimination between formation layers. However, they do suffer from the disadvantage of being located, by necessity, tens of feet behind the bit. The mud motor needs to be nearest the bit, and above that, near bit survey tools, to give the driller earliest possible indication of direction change. In a certain slim hole tool, the formation evaluation sensor is approximately 25 feet behind the bit, which reduces the effectiveness of the information considerably. The common problem he distance travelled by the bit between the time when the formation boundary is crossed and the time when the fact of the crossing becomes apparent is a problem. It is especially significant in layered and thin formations or in formations that don’t have suitable markers to distinguish between the different layers or boundaries, situations that are very common in re-entry drilling. Figure 2a. shows a conventional formation evaluation sensor located in the drilling BHA, a distance, LSense from the bit. When the bit crosses the boundary from one formation to another an additional Lsense ft will need to be drilled before the change in formation is visible to the sensor. If the thickness of the formation is of the same order then it will not be possible for the driller to execute a steering action before the drillbit has left the formation of interest. This has a cost, in terms of lost production and time wasted drilling unproductive formation. Were formation discrimination available at the bit, then this depth lag could be eliminated. The latest generation of coiled tubing drilling BHAs provide the data to make this new geo-steering method possible. A solution to address past challenges To understand how this new geo-steering method works, let’s take an analogy. Picture yourself a passenger in a moving car. Even with your eyes closed, you know the type of road you’re travelling on (freeway, city street, country road) by the road noise you can hear. Consider now a motor turning a drill bit which drills a hole in a sample of rock. We can measure the power input to the motor as the hole is drilled to gain an understanding of the type of rock we’re drilling. If it was an electric motor we would simply measure the voltage applied and the current flowing during drilling and multiply them to get the instantaneous power. For a positive displacement mud motor it’s slightly more complicated, but it can be done. If differential pressure and flow rate can be measured then, given knowledge of principal operating constants for the motor, an expression for power in terms of pressure and flow rate can be written. If we were then to integrate this power as the hole progresses we would have a value of Energy expended per foot of hole drilled and would therefore have a relative indicator of the changes in formation being drilled. To view the rest of this please contact us
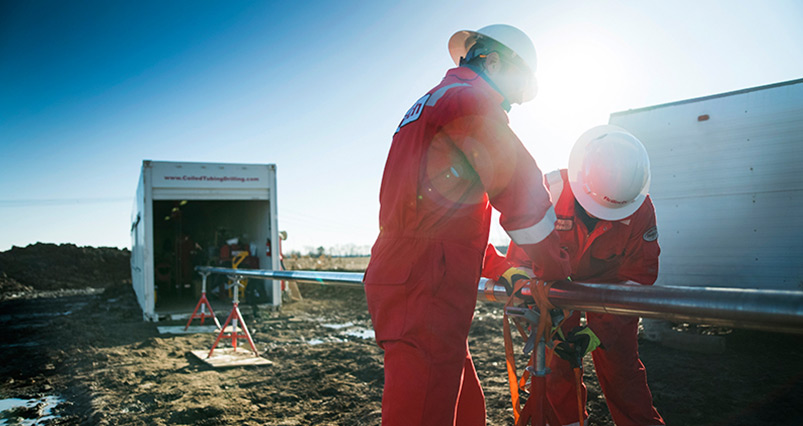
1506859200000
Combining Several Proven Drilling Technologies Makes A Compelling Value Proposition For CTD
Re-entering wells in declining fields is viewed as challenging yet increasingly necessary. But when they are carefully planned and managed, advanced methods such as directional coiled tubing drilling deliver reduced costs and increased yields when compared to traditional methods, making capturing reserves in declining wells much more viable. By Clare Miszewska-Hall, Head of Global Sales & Marketing at AnTech Seventy percent of all oil and gas production comes from mature fields. This figure highlights the need for operators to increase the productivity and efficiency of their declining fields while also minimising environmental impact and surface footprint. The need becomes even more pressing in a market where market forces are driving down prices. While there is much to be gained from looking at small incremental changes that add up to a larger overall benefit, sometimes there are better gains to be had from looking at bigger solutions and utilising technologies that are in many cases still perceived to be at the cutting edge. Taken individually, such technologies offer considerable advantages. They can offer even greater opportunities when combined. For example, by combining horizontal drilling and underbalanced drilling (UBD) with the advances in coiled tubing technology, it is possible to drill multi-lateral wells with directional coiled tubing drilling (DCTD) allowing an operator to capture significant extra value out of known reserves, making maximising returns from declining fields a viable proposition. Indeed, when applied correctly, such technologies can reduce costs by up to 30% and deliver increased production rates when compared to traditional methods. In this article we will look at these techniques in isolation and in combination and understand why they have such potential to deliver. We will also look at why they are still viewed as niche technologies and look at how to mitigate the risks they are seen as having. The technologies under consideration Before we look at the risks that need to be mitigated when looking at utilising advanced drilling techniques, let us take a moment to look at what the technologies are and the benefits they deliver. Multi-lateral drilling The use of multi-lateral drilling has grown substantially since the mid-1990s. It enables an improvement in reservoir production and a lesser environmental footprint for a minimal increase on drilling and completion costs, most noticeably in projects where well cost is traditionally high, such as in deep water, offshore or Arctic projects. The concept builds on that of horizontal drilling and involves multiple wellbores connected to a single main bore. Underbalanced drilling (UBD) Underbalanced drilling increases well productivity and recovery, reduces drilling problems such as differential sticking and removes damage near the wellbore. The technique maintains the pressure in the wellbore at a lower level than the static pressure in the formation being drilled. It is commonly used in conjunction with the other advanced techniques detailed here. The technique is suitable for most fields, although there are geological, safety and environmental concerns that may prevent its use in some situations. Coiled tubing drilling (CTD) Directional coiled tubing drilling has a history of around 20 years but remains a niche technology in all areas but Alaska and Saudi Arabia. It combines coiled tubing and directional drilling and means bottom hole assemblies can drill directional, S-curve and horizontal wells. Advantages such as the amount of real-time data received from the BHA being significantly more than on a mud pulse system or EM system enable drilling directors to optimise on the fly meaning it delivers increased efficiencies and rates of return. Using this technique is proven to enable a reduction in drilling times of between 30% and 60% and a 30-40% reduction in cost compared to conventional jointed pipe drilling. Understanding the risks As the figures in the preceding section show, there are some attractive numbers surrounding the use of these technologies. It begs the question why, when they offer such a wealth of gains, have they not been immediately and widely adopted to improve rates of capture from declining fields? In the case of the technologies outlined above the reason can be simply stated as the propositions seeming too risky thanks to the combination of the level of upfront investment required and the complexity involved. However, with the right modelling tools and expertise, both concerns can be overcome. Let’s delve into them in a little more detail and start to look at what’s involved. The issue of too much cost There is no doubt that the upfront investment involved in using these advanced technologies either in isolation or in combination looks unfavourable at first glance when compared to the upfront costs involved in a traditional set-up, in many cases to the extent of discounting it altogether. However, to do this is to lose sight of the bigger picture: which are the gains to be achieved. To regain perspective, it is important to model the most significant upfront costs and the projected future revenue in order to see when an intervention will break even, the subsequent future revenues and the IRR for the project. In doing so, the upfront costs can be put into the context of the potential rewards, enabling a true assessment of the costs to be made. In essence, the calculation that needs to be made is one that generates a graph such as the one in Figure 1. Figure 1 – Example cashflow before and after CTD intervention This graph can be generated by modelling four factors: the production increase that might be expected by drilling a horizontal (i.e. a multi-lateral) well instead of a vertical well, the oil price, the total cost of the intervention and the decline curve of the well. Productivity Improvement Factor Horizontal wells contact more of the reservoir so they can give higher productivities in laterally extensive reservoirs. The extra benefit of drilling a horizontal well can be estimated by using the Productivity Improvement Factor (PIF). This compares the initial productivity of a horizontal well to that of a vertical well in the same reservoir during early time radial flow. The PIF is defined in Equation 1 where L is the length of the reservoir; h is the height of the reservoir; kh is the horizontal permeability of the reservoir and kv is the vertical permeability of the reservoir. Equation 1 As a rule of thumb, a PIF of between 3 and 4 allows for the undoubted uncertainties involved in drilling a horizontal well, especially for the first time. Note that the PIF assumes overbalanced drilling. While it is certainly true that underbalanced drilling (or even at-balance drilling) can greatly increase the rate of production and reduce the drilling time, by assuming overbalanced drilling there is an element of caution built in to the calculation. The Oil Price:The oil price will always be a best guess, although it is always useful to alter this variable and understand how marginal (or not) an intervention is likely to be on the payback time. Bear in mind that the shorter the payback time the lower the risk because there are fewer opportunities for oil price fluctuation. Total Cost Of Intervention:The total cost of the intervention involves a clear-eyed, rational assessment. Put simply, knowing the maximum amount it would be viable to spend on a well to achieve the desired payback will dictate the technologies that are available. On some older wells an intervention will simply not be economically viable. We look at some of the factors that will affect this cost in the next section. The Decline Curve:The decline curve takes into account the fact that all wells decline over time. The precision with which this figure is calculated is not especially important when modelling the numbers, what is important is that the decline is considered in order to avoid over-optimistic projections. A decline curve that reduces production to a certain percentage after the first year will provide the necessary insight; known field data might provide greater reassurance as to the realism of the numbers. This modelling provides a way to understand the high initial investment against the likely returns, thereby setting the investment in context and giving it greater appeal. Now let us turn to the other concern with investment in newer technologies. To view the rest of this please contact us
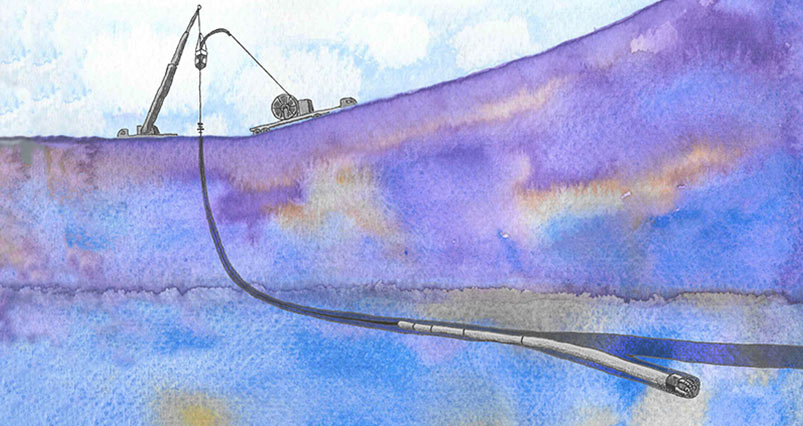
1504612800000
Drilling Multilateral Wells Using Coiled Tubing
By Adam Miszewski, AnTech Ltd. The oil and gas industry is constantly driving to reduce capital expenditure and increase economic recoverability while minimising environmental impact and surface footprint. By combining the three advanced drilling techniques of multi-lateral drilling, underbalanced drilling (UBD), and directional coiled tubing drilling (CTD), an operator can capture significant value out of known reserves. To be classified as a multi-lateral well, the well must have one or more additional wellbores branching off from the main wellbore. The fundamental principles behind maximising return on investment from a well are: reducing capital expenditure and maximising well productivity. The highest well productivity is achieved through maximising reservoir contact per well/surface slot and minimising reservoir damage. Multi-lateral drilling reduces capital expenditure through drilling multiple reservoir sections per surface slot, and also, increases reservoir contact per surface slot. UBD minimises reservoir damage which maximises the productivity of each lateral. CTD is inherently set up for underbalanced operations (UBCTD) and CTD bottom hole assemblies (BHAs) can achieve high build rates, of up to 50 deg/100ft, to allow for multiple targets to be accessed from the motherbore. Viewed separately, it is easy to see how the three drilling technologies combine to make a compelling value proposition for an operator. BHA Selection consideration when drilling multilaterals A directional CTD BHA consists of a coil connector, a cablehead, an electric or mechanical disconnect, a downhole orienter, a sensor package, a motor or turbine with a bent housing, and, of course, a drill bit. Drilling directionally on coiled tubing is very similar to conventional slide and rotate drilling on a rotary. As coiled tubing cannot be rotated from surface, all the rotation needs to be carried out downhole through the orienter. The rotating orienter allows the toolface to be set from surface or for the motor to be rotated to drill a straight hole. High quality service companies can also provide additional BHA modules such as a gyro module for orienting a whipstock and for drilling in the presence of magnetic interference, immediately after exiting the casing. To read the full article please visit: Hart Energy
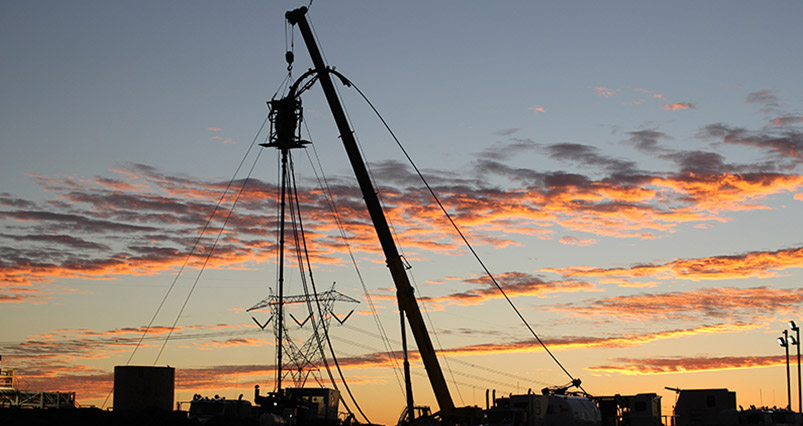
1488369600000
Squeezing Out That Last Drop Of Oil Using Underbalanced Coiled Tubing Drilling
Underbalanced coiled tubing drilling can help extract more production from existing wells, reduce project unpredictability and economic risk, and contribute to increased, efficient, long term hydrocarbon extraction. As human beings, we suffer from loss aversion, where we are more afraid of loss than we are motivated by making a gain. In the oil and gas industry where the sums of money involved can be high and the consequence of failure can be catastrophic this tendency is exaggerated by the fact that costs are guaranteed but rewards can be uncertain. This leads us to define work in terms of definite costs rather than possible gain. For example, drilling is often measured in terms of cost per foot rather than in terms of cost per barrel produced. In doing so, we can miss out on getting the best return from our assets. Aversion to risk means that the oil and gas industry has historically taken many years to take on-board new technologies even though they have demonstrable benefits. Directional, underbalanced, Coiled Tubing Drilling is one of the technologies that ticks all of the boxes in terms of benefits but has remained a niche application. Multi-year projects have been on-going in Alaska since the early nineties and in Saudi Arabia since the middle noughties and there have been other, shorter term, projects both on land and offshore. These have proved successful as demonstrated by their long-term nature. Uneconomic projects don’t last very long. Despite there being hundreds of thousands of depleted wells where the benefits of underbalanced Coiled Tubing Drilling are very applicable, so far, the technology has not entered the mainstream. There was a time when other technologies were also looked on in the same way. These days nobody thinks twice about horizontal drilling. In fact, some younger drilling engineers might be forgiven for thinking that the only way to drill a well is horizontally. Despite the technology being introduced in the early 1990’s it took until 2010 for horizontal wells to really take-off and, these days, 77% of the most prolific well in the US are horizontal. Coiled tubing has made steady advances in terms of reliability and services and is now considered mainstream technology. It takes a market jolt, like the one being experienced during the current downturn, to spur the adoption of newer technologies. In boom times, costs rise and this doesn’t help the introduction of new technology because the cost savings can get swamped by the increasing prices. One thing that characterizes all of these technologies is the fact that they all cost more than the technologies that they replace, but the increase in productivity ultimately makes the extra investment worthwhile. In no case would anyone, especially not an accountant, have advocated their introduction if they had just considered their day rate cost alone. So, we need to have a way of evaluating the benefits of new technology in a way that gives a fair weighting to both the benefits and the costs. Overlooked Production In the current low oil price era, it is an attractive option to re-work existing wells with an intervention to increase production. Re-working a well at least takes away the uncertainty of whether there is a productive oil or gas zone to be accessed, which can be a risk with a new well. One, potentially very rewarding way is to cut a window in the production casing of a vertical well and to drill horizontal laterals in underbalanced conditions with coiled tubing. In some cases this technique has increased production by a factor of five. Directional Coiled Tubing Drilling brings together horizontal drilling, underbalanced drilling and coiled tubing in a way that takes advantage of all three technologies. Coiled tubing is a technology specifically designed for working under pressure so it is ideal for underbalanced drilling where maintaining the correct pressures is critical to protecting the reservoir. In fact, Coiled Tubing Drilling is the only way to ensure that the well is kept underbalanced at all times because the operation does not need to stop to make connections. With underbalanced drilling come the benefits of increased drilling speeds, reduced lost circulation and differential sticking problems and, a key advantage, the reservoir is protected from formation damage. Reduced problems translate into reduced project risk which is a key requirement when the efficiency of a project is vital to its economic success. But interventions cost money and underbalanced drilling with coiled tubing is more complex and less familiar to most. There is a natural tendency to say ‘how much will it cost’ before asking the question ‘what’s the pay-back’ which is what really matters. In the process, economic opportunities might be ignored. Fortunately, it’s relatively straightforward to combine the most significant factors in terms of cost and, importantly, revenue to evaluate whether an intervention is worth doing or not. By taking into account the timing of both costs and future revenues it is possible to see when an intervention will break even, what future revenues will be after that point and consequently the IRR for the project. This is something that can be done with a simple spreadsheet model and it helps to concentrate the mind on the return on investment before considering what it is worth spending to achieve that return. The Forward Looking Model The model used is dependent on four factors: The production increase that might be expected by drilling a horizontal well instead of a vertical well.The oil price.The total cost of the intervention.The decline curve of the well. The Production Increase:The Productivity Index is a function of the length of reservoir drained by a well. Horizontal wells contact more of the reservoir so they can give higher productivities in laterally extensive reservoirs. As an estimate of the extra benefit of drilling a horizontal well you can use the Productivity Improvement Factor (PIF) which compares the initial productivity of a horizontal well to that of a vertical well in the same reservoir, during early time radial flow. The PIF is defined as: Where, L is the length of the reservoir; h the height of the reservoir; kh the horizontal permeability of the reservoir; kv the vertical permeability of the reservoir. On this basis, assuming that horizontal and vertical permeability are the same, and that the reservoir is 40ft thick and the horizontal is 400ft long, then the PIF would be 10. This is a theoretical value and in practice, based on historical data, a PIF of between 3 and 4 should be considered to allow for the uncertainties inherent with drilling a horizontal well, potentially for the first time. The PIF assumes that the wells will be drilled overbalanced and that underbalanced drilling would not offer any further production increase. Underbalanced or at-balance drilling can greatly increase the ROP when drilling and therefore reduce the drilling time. Coiled Tubing Drilling is well adapted to UBD. The Oil Price:The oil price should be taken on a best-guess basis. It is a variable and it can be changed to see the sensitivity of the pay-back and therefore the risk that can be tolerated. Clearly, a higher oil price will allow a shorter payback time and a lower oil price will extend the payback time. If you had a crystal ball and could predict future oil prices, the value could be varied over time but in most cases, short term pay-back is the governing factor in deciding about an intervention. The Total Intervention Cost:This is the value that is effectively being determined. It can also allow for production during the drilling process. Better technology that will produce a better result may be just the ticket, but it needs to be affordable for the well under consideration. Some wells will be passed the point where an intervention is economically viable. Knowing the maximum amount that can be spent economically on a well to achieve the desired pay-back dictates the intervention that might be considered and the subsequent discussions with the appropriate service companies. The cost of chasing a wild goose is not negligible. The Decline Curve:Every well is different but they will all decline after initial production. So, being precise about the exact form of a decline curve is not particularly important when doing comparative calculations. Its main purpose is to avoid grossly over or under-estimating the returns over time. A decline curve that exponentially reduces production to a certain percentage after the first year is as good as any but this can be easily changed based on known field data. To view the rest of this please contact us
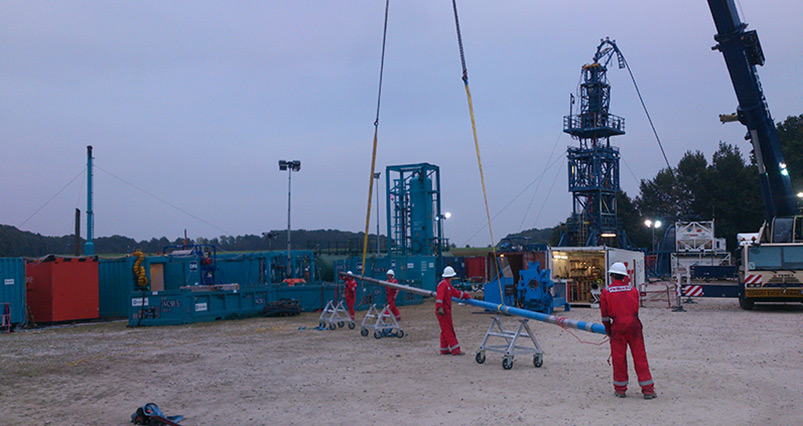
1488369600000
Solving The Blind Spot Problem With Re-Entry Coiled Tubing Drilling
By Toni Miszewski, AnTech Ltd. A New Directional Sensor Solves The Blind Spot Problem When Exiting Casing While the main drilling attention over recent years has been about new unconventional and deep water wells, nearly 70% of the worlds hydrocarbon production comes from declining fields. There is a compelling economic case that extracting more from known reservoirs is a better idea than the cost and risks of a new project. In practice, working over mature fields involves various enhanced oil recovery (EOR) techniques and re-entering wells to drill horizontal laterals from a window cut in the existing wellbore. An established, if not yet widely adopted technique to do this is to use Coiled Tubing Drilling (CTD) to drill in underbalanced conditions. The Declining Well Challenge An efficient operation is an essential requirement for working over wells that may have a limited production capacity but at the same time still have significant unrecovered reserves. It is not realistic to expect a multi-year payback time especially with a low and uncertain oil price. Drilling in the right direction is a fundamental requirement of directional drilling and drilling in the wrong direction, even if the error is only small, is one of the easiest ways to reduce efficiency. This is surprisingly easy to do because of the distorting effect of steel casing on the magnetic sensors of a CTD BHA which creates a blind spot when first exiting the window. This effect may extend as far as 20ft from the vertical casing. Whilst this is a problem for all casing exits, the problem is worse for CTD operations. There is often limited vertical depth between the window and the target formation so high build rates are required and this leaves little room for error. To read the full article please visit: Hart Energy
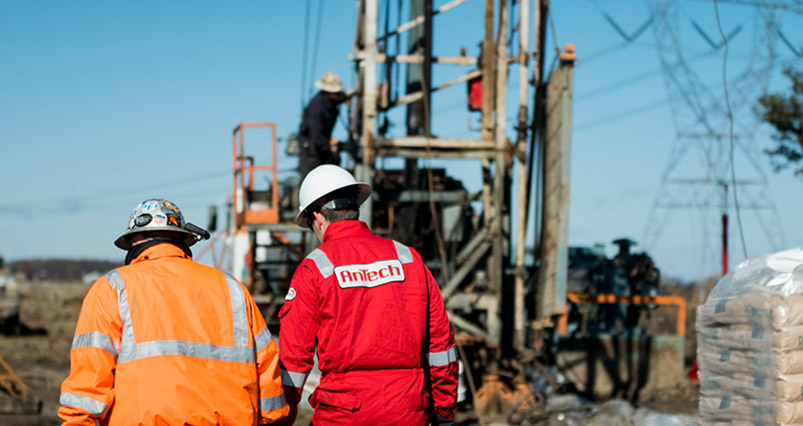
1485950400000
Delving Deeper Into DCTD. Andrew O'Brien explains more
Andrew O’Brien, AnTech,UK, explains why CTD applications are so relevant to today’s oil and gas industry. Directional coiled tubing drilling (DCTD) has become a mainstream drilling activity in numerous parts of the world and modern DCTD is nearly 30 years old. Awareness of the reasons for using DCTD and its range of applications is, however, sometimes limited. DCTD has been trialled or used in many areas by most medium and larger operators, but has tended to be concentrated in specific locations or used by operators who have built up experience with the technique. Most will be familiar with the main applications of DCTD: Brownfield through tubing re-entry work, underbalanced drilling and short radius profiles. However, there are some other less well known reasons for selecting the technology as well as several new applications that have moved from the drawing board into development, and will soon be available to the industry, further increasing the scope and capabilities of DCTD. A Closer Look At Directional Coiled Tubing Drilling DCTD technology combines coiled tubing drilling with directional drilling, utilising a steering assembly with an ‘orientor’ to navigate the bit in the required direction and inclination. Modern DCTD has evolved significantly since its origin in the early 1990s, with orientors now powered with an electric logging cable run inside the coil tubing, which also conveys MWD/LWD signals between the downhole tools and surface. This wireline enabled coil allows for real time adjustment of orientation, while the internal e-line cable allows high rate, real time drilling and logging data to be transmitted to surface without drilling or flow interruption, as there are no pipe connections during drilling or tripping. The absence of pipe connections reduces time spent running and pulling pipe, as well as time spent taking surveys, and means that two phase fluid flow (if used) is uninterrupted. Reduced handling of pipe, along with a continuous circulating system, increases safety at the wellsite, resulting in fewer manual handling incidents and NPT. These characteristics make DCTD especially suitable for pressure sensitive shales or depleted wells requiring underbalanced operations, underground gas storage wells that require minimal skin damage and unconventional gas wells. Some CTD bottom hole assemblies are short and can drill very high builds and turns, making them ideal for targeting complex wells with difficult to reach, faulted or thin producing horizons. The precision and flexibility that this technology offers frequently means that many horizontal laterals are drilled from the same original well bore, increasing the wells drainage area by producing from multiple formations in the same reservoir. Moreover, the footprint of a CTD spread is significantly less than a conventional rig spread for the same application. This low environmental and noise impact often allows the technology to take precedence over conventional rigs in areas that have high environmental or land owner concerns. The smaller rig is also suitable in Arctic zones where the rig and work area may have to be permanently covered or heated. Another key consideration is cost. By re-entering a well and sidetracking through existing tubulars, DCTD saves the significant cost of pulling a completion or re-drilling the upper sections in a new well. Additionally, existing pads and facilities may be reused, resulting in further savings. As onshore and offshore fields mature and have junked or poorly performing wells, the number of wells that can be ideal candidates for re-entry and DCTD campaigns are rapidly increasing. It should be noted that Brownfields hold the most reserves worldwide and the current recovery factor is estimated as little as 30%. In the current climate, many operators are looking to improve and extend existing production with enhanced oil recovery and techniques such as DCTD for re-entry of wells, rather than drill completely new wells. CTD Case Histories Around The World To highlight the variety of applications and reasons for using DCTD the following case histories have been included; Dubai, Margham Field Why:Increased gas feedstock was required to supply increasing energy use, to reduce liquid feedstock use and reduce CO₂ production. Details: An initial four underbalanced (UB) wells were drilled after a study had concluded that the only practical way of increasing drainage in the highly fractured depleted field was high angle re-entries from existing wellbores. Wells were 150˚C and with high H2S levels. The drilling fluid was Nitrified water with foam sweeps. Results:Initial wells showed a 73% net increase in production of gas (over non-intervention field production rates). A second phase of four wells showed a 125% increase in production. Three final wells were then rejuvenated. In total, fifty laterals were drilled on the eleven wells (one well with eight laterals alone). When drilling UB, flowing the wells while drilling provided US$170 million dollars of condensate/ gas production. The project cost was paid back in 2½ months of field production due to additional revenue from producing whilst drilling. Due to a high safety focus and detailed planning, 328 000 man hours were worked without an LTI. Figure 1 - Advantages of coiled tubing drilling. USA, Pennsylvania Why: Improved field maintenance on two gas storage reservoirs. Previous conventional and unconventional attempts to stimulate the wells in the fields were not satisfactory and the reservoir thickness was only 4 ft to 9ft. One location required a rig with a small footprint and low environmental impact. Details:Previous field maintenance methods tried had not showed a significant improvement in skin factor. UBDCTD improved deliverability. Results:One well was drilled with up to 84°/100ft build with UB and freshwater/polymer plus N2 to obtain a 180ft lateral, resulting in a 840% increase in gas deliverability. The second field drilled a 698ft lateral with 650 psig underbalance and 28˚/100 ft build rates, build rates were reduced to allow a completion. Testing three months after completing indicated that the horizontal well extension had yielded an 8000% increase in deliverability from the well. Offshore Malaysia Why: Small platform constraints. Tapping in to bypassed reserves. Details: The platform had minimal space and could not undergo any changes or crane upgrades, so DCTD was considered suitable. Wells were designed to use the existing completion in order to reduce time and cost. Results: Four wells were drilled with deep kick off points to avoid problematic shale sections and were successfully completed. Lessons learnt from the first two wells greatly increased the performance in the later wells. Saudi Arabia Why: Increased reserves: wells drilled UB with DCTD to remove the requirement for a well kill and short radius to avoid problematic well sections and numerous differently pressured zones. Details:Short radius wells with 2000 - 3000 ft laterals were drilled, removing the requirement for traditional long radius profiles and well kill complications. DCTD has simplified wells and reduced difficulties above the reservoir.KSA has avidly adopted the DCTD technique since this case history. Results:Complex multilateral wells are routinely drilled with very high H2S levels (BHA’s are pressure deployed) and at very high temperatures approaching HPHT well levels. Hybrid DCTD rigs have been used with great success in KSA since 2010 . . . To view the rest of this article please contact us
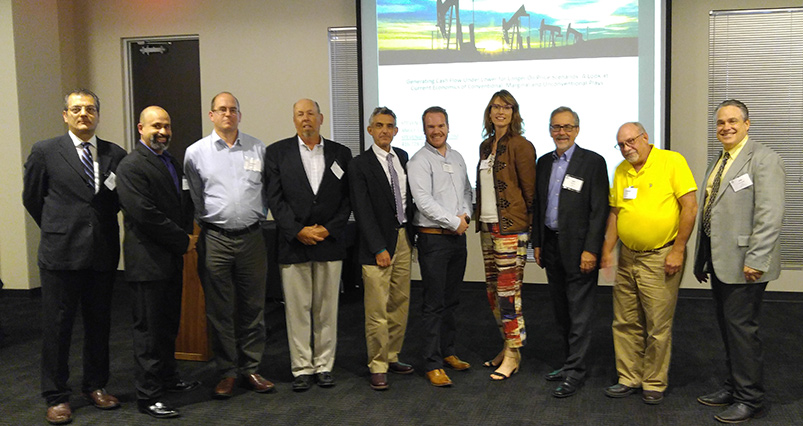
1461758400000
AnTech Presents At AAPG New Thinking Event
In May, AnTech was invited to present at the American Association of Petroleum Geologist’s (AAPG) latest workshop. The event titled ‘New Thinking and Value Propositions in Exploration and Production: Pro Active Steps Now’ was held on the 17th and 18th May, at the Norris Conference Centre, Houston. The conference featured over fifteen presentations from a variety of operators, consultants, and service companies and headline names included Halliburton, New Horizon Exploration, Pressure Pumping and Riverford Resources. The aim of the two day workshop was to proactively explore opportunities and learn about the holistic value proposition of revitalising old wells, which is highly relevant in today’s low price environment. An extensive range of topics were covered during the conference, including a presentation from our very own Richard Stevens, AnTech’s Coiled Tubing Applications Engineer. Richard’s presentation explored the opportunities and the value proposition associated with Coiled Tubing Drilling. The key points from his presentation were: Operators have been forced to re-evaluate the economic viability of their reserves as oil in the ground generates no revenue.However, getting oil from the ground in a sub 50 USD/bbl market and making a profit, is providing a highly stimulating challenge to a generation of engineers and geologists accustomed to twice that market value.Innovative technologies such as Directional Coiled Tubing Drilling provide opportunities and can help revitalise oil wells.Directional CTD Bottom Hole Assemblies are being deployed in order to drill new wells but more importantly, to re-enter and extend existing wells by adding multi-lateral branches and extensions.More complex and larger holes of up to 8-1/2" are being drilled, enabling operators to make the most of their existing reserves.Operators should consider the holistic value proposition of an intervention and the lifecycle of their resources. The event was a great success and attracted engineers, geologists, geophysicists, land professionals and entrepreneurs from across the oil and gas industry. We would like to thank Susan Nash, Director of Innovation & Emerging Science and Technology at AAPG for the kind invitation to present at the event. To find out more about the workshop or AAPG, please visit: AAPG
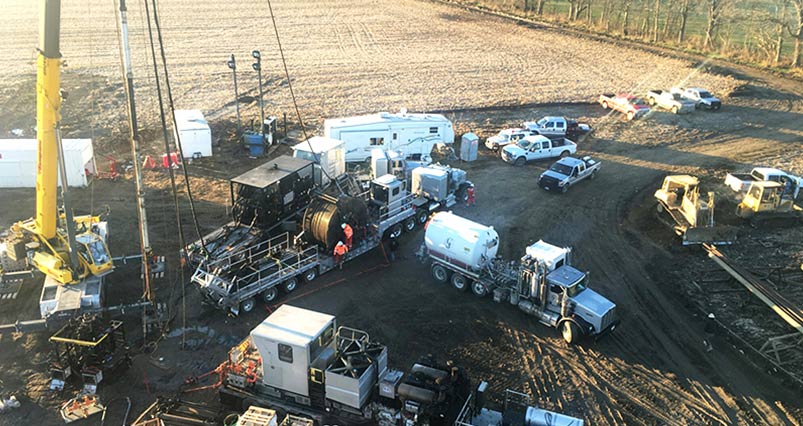
1459512000000
How New Technology Offers One Solution To Low Oil Prices
There is no doubt that current oil prices are presenting a difficult challenge to the industry and stretching people' creativity when thinking of solutions. Slashing costs, which means people and equipment, makes for more dramatic headlines but simple efficiency gains also have their part to play as the industry adjusts to the new reality. Extracting more from existing wells has an immediate effect on efficiency. A clear example is the migration of the shale operators to the most productive wells in the field that has seen production per well increase at the same time as the number of wells that are drilled dramatically decreases. Another way of increasing efficiency is to apply technological solutions that access more of the reservoir but from an existing wellbore or which provide more detailed well information which can optimize the amount of hydrocarbon extracted. Two technologies which fit the bill are directional coiled tubing drilling and permanent monitoring with fiber optic sensors. Both of which were in their formative phase in the early 1990’s but which have now developed into established products. Accessing more of the reservoir with Directional Coiled Tubing Drilling The current sub 40 USD/bbl oil market is putting a huge amount of pressure on operators to maximize the returns on current assets and to minimize the operational and financial risk associated with accessing these reserves. Re-entering old wellbores and sidetracking to access new reserves in known reservoirs is a low risk way to increase cash flow and return on investment from an operators assets. Directional Coiled Tubing Drilling (DCTD) is a well-established technology for doing this. Over the last three decades significant advances in equipment reliability, metallurgy and the experience levels of personnel has made DCTD a very attractive method of re-entering wells. Operators and service companies can focus on delivering productive wells effectively rather than dealing with technology issues. DCTD can also provide significant that are applicable to drilling new wells or for re-entry. One of the most significant advantages of DCTD is it’s suitability for – underbalanced drilling allows the formation to produce oil and gas while drilling which means that the formation is not damaged like it is in overbalanced drilling. This reduction in formation damage can lead to significant increases in the amount of oil produced from each well drilled. Figure 1 - Example wellpath for a sidetracked well. The long horizontal sectionincreases the production of the well over that of a vertical well. More complex operations such as multi-lateral branches, extension and larger hole sizes are being drilled, enabling operators to make the most of their existing reserves. Consequently, directional coiled tubing drilling BHAs are being deployed around the world in order to drill new wells and extend previous ones by accurately targeting pockets of oil and gas reserves. Successful drilling programs are ongoing in Saudi Arabia, Alaska and Australia as well as other places. The Introduction of COLT and POLARIS Ten years ago, AnTech combined mechanical, electronic and software engineers and the and DCTD Bottom Hole Assemblies (BHAs) were created. The COLT Measurement While Drilling (MWD) BHA is a 3.192” OD BHA which is steered magnetically. The POLARIS MWD/GWD BHA is a 5” OD BHA which is steered either using magnetic sensors or a gyro. The BHAs are run on Coiled Tubing with 7 conductor electric line inside the tubing (also known as e-coil). The connection to the BHA from surface via a cable allow real-time telemetry and very high data rates. This capability allows for extremely accurate wellbore placement thereby increasing the chance of success on a project. The two BHAs are short – under 40ft in length – which allows them to be deployed above the blow out preventers. This means that the well can be closed in while the BHA is made up to the coil and pulled into the lubricator. The well is then only opened up once the complete pressure control envelope in place. This increases the safety of operations and allows for simple underbalanced deployment. The short BHA length also has the advantage of minimizing the distance between the bit and the survey tool meaning that the directional control is improved further. Both BHAs recently demonstrated their technical and commercial viability in two recent projects. POLARIS was used in France to sidetrack a well and drill a new lateral to increase production from the well. COLT was used in the Appalachian Basin to sidetrack a vertical wellbore and drill a lateral to turn a dry well into a producer. Both projects were a success with the operators achieving their objectives. Distributed Sensing with Fiber Optic Monitoring Also in the early 1990’s permanent well monitoring started to become more widely used (price of oil at the time, $20). The systems in those days were electrical and provided point measurements of usually pressure, temperature and flow. These days, in addition to the electrical systems which have become cheaper and more reliable, a new generation or fiber optic sensors is available to operators. The nature of fiber optic sensor systems is that they can provide distributed measurements which means that if they are measuring a parameter such as temperature, the temperature can be recorded with a 3ft precision along the whole length of the cable. This provides a whole new dimension of visibility about the wellbore that was previously unavailable. Pressures, acoustic and seismic signatures can all be measured in this way. When these fiber optic cables reach the surface, they need to be terminated and connected to the surface instrumentation. Keeping optical losses to a minimum is vital to ensure that the resolution of the sensors is not affected. Delicate optical fibers, no more than the thickness of a human hair present a challenge in an industry where a pipe wrench is a more common tool than a fusion splicer. As a result a whole new range of equipment has had to be developed to adapt super-precision assembly to the rugged environment around the well head. This is also a hazardous area environment were electrical equipment needs to conform to conform to international standards for use where explosive gases are present such as IECEx. AnTech’s dedicated products division, is an expert and well-known supplier of Wellhead Outlets and has developed a whole new range of fiber optic products which continues to grow. Demands for equipment that can safely allow fiber optic connections to downhole gauges in high temperature and pressure environments can now be met. AnTech has recently launched the Type-F range of fiber optic wellhead outlets which incorporates their proprietary feedthrough that is designed to API 6A standards. Additionally the Type-F range allow for excess fiber to be stored so that multiple attempts can be made at connecting, whilst protecting the delicate fiber. With in-house design engineers, AnTech can also deliver standard and customised fiber outlet solutions for most wellhead connections and downhole cables. Figure 2 - AnTech's Type-F Wellhead Outlet Furthermore, design and development on an explosive atmosphere certified Fusion Splicer has begun and this will in turn help complement the Type-F wellhead outlet range by safety splicing delicate fiber at the wellsite. Conclusion Change can be a challenge in an industry that is historically cautious about change. And this is for a good reason, the risks of failure with new technology are high so the benefits need to be significant. But the abrupt re-set of the industry means that doing the same thing and expecting a different result is not an option. and are two technologies that have shown their worth over time and now might just be the time when these innovations may offer an economic solution in a turbulent and challenging market. Published in Hart's E&P Magazine - March 2016
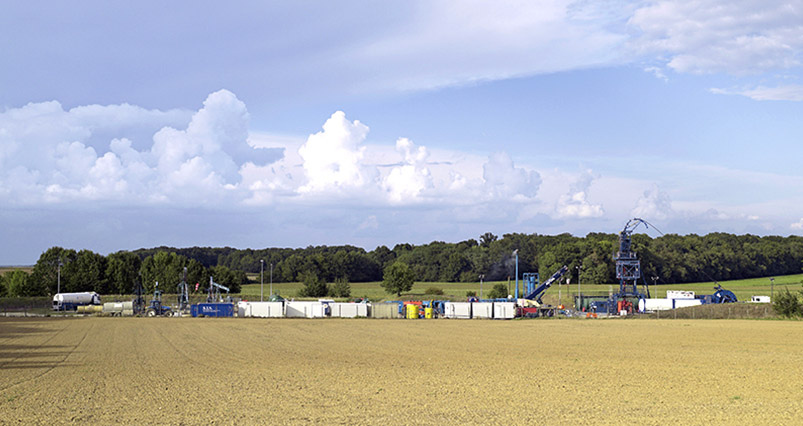
1457006400000
Exploring The Value Of Reserves. Re-examining Reservoir Management
In today's world of weaker oil prices and declining production output of oil and gas reserves, operators are re-examining their reservoir management efforts. Globally, operators are facing the challenge of optimising the performance of not only new wells but also existing reserves whilst reducing costs. As a consequence there is an increasing need for an economic means to tap bypassed pockets of oil and gas reserves and bring old wells back into production. The Challenge for Operators Improving production output from mature fields often presents challenges and as a result innovative technologies must be used to overcome these complexities. The critical factor when evaluating a potential intervention is Return on Investment (ROI). It is crucial for operators to understand the characteristics and possibilities of their wells prior to making any decisions. The cost of the intervention and the potential increase in production after it has been performed are important factors that need to be considered. The goal for many operators is to improve ROI by initiating production as soon as possible through precise drilling whilst keeping a watchful eye on operating costs. The Challenge for Operators Coiled Tubing Drilling (CTD) is an attractive alternative to conventional methods for many demanding and more challenging operations. CTD technology has been used effectively for more than two decades and saw an increase in its use in the mid-1990s, during which time a large number of wells were drilled using this technique. Its mainstream popularity decreased at the end of this period due to the economic downturn and the fact the applications for the technology were not fully understood. However, CTD still remains active in Alaska, Russia and Saudi Arabia and there have been significant advances in the industry’s understanding and development of the technology. Increasingly Complex Operations At present, awareness and uptake of CTD is increasing amongst operators, who can see the tangible that the technology provides. The most significant advantage that CTD can offer is the ability to drill underbalanced, whereby the pressure of the wellbore is lower than the pressure of the formation being drilled. This protects the formation and allows the well to produce during drilling. It also decreases the risk of differential sticking and increases the Rate of Penetration. Furthermore, the coiled tubing has additional benefits over conventional jointed pipe drilling. The coil reduces manual handling as there is no need to make up pipe joints. Drilling is continuous, apart from wiper trips, which in turn helps reduce the costs and consequently increase the value in the drilling program. Directional CTD Bottom Hole Assemblies are being deployed around the world in order to drill new wells and extend previous ones by adding multi-lateral branches and extensions. Larger holes of up to 8-1/2’’ and deeper wells are also being drilled, enabling operators to make the most of their existing reserves. The Full Picture A meaningful way of measuring the value of a drilling program is to define it in terms of cost/barrel produced, rather than cost/foot or cost/day, as this is the direct measure of ROI. It takes into account the increase in production resulting from the intervention. That being said the other measures do give a useful metric when evaluating a project. A case study on the Chittim Ranch in West Texas (i), showed a 60% decrease in the average time to complete a well when compared to conventional rotary rig drilling. These conclusions were drawn after 233 wells were grass-root drilled. The wells were vertical and overbalanced. The decrease in time translated into a 33% cost reduction per well when compared with the most recent conventional drilling data from the area. The difference in cost was adjusted to take inflation into account. Recently, AnTech has developed a proprietary financial model that analyses the ROI of an intervention for new and existing wells. By utilising existing oil or gas production data and the Approval for Expenditure (AFE) of the operator, the model can predict the payback time of an intervention operation. Wells produce at their maximum rate at the start of their life cycle and naturally decline over time as pressure decreases and often water cut increases. As a consequence of this decline, the wells reach a point when it is no longer profitable to produce. Before this point an intervention should be evaluated whist there is still sufficient cash being generated from the production. The payback of such an operation depends on several factors that are taken into account in AnTech’s model. The Components behind the Model The cost and production components of an intervention method are too intertwined to allow a hand calculation to provide sufficient information to evaluate a project. Nowadays, with more complex operations, it is important to evaluate the total operational cost versus the total benefits of an intervention whilst at the same time allowing for the production decline over that same period. AnTech’s model utilises the Productivity Improvement Factor (PIF)(ii), which compares the initial productivity of a horizontal well with the productivity of a vertical well in the same reservoir. The PIF is defined as: where L is the length of the producing section of the horizontal well h is the length of the producing section of the vertical well kv is the vertical permeability of the reservoir kh is the horizontal permeability of the reservoir kv/kh quantifies the permeability anisotropy (iii) It can be seen that the PIF depends directly on the length of reservoir drained by a well. This is one of the reasons why a horizontal well can give higher production in laterally extensive reservoirs. From the formula, it can be seen that a horizontal well (L>h) will have a bigger PIF than a vertical well (h>L), if the permeability anisotropy is 1. In practice, and this is borne out by actual well data, this increase in production may not be fully realized for a variety of reasons one of which is drilling damage. Where this is the case, underbalanced drilling can often prevent this damage and increase the success rate of wells that might be difficult to drill due to lost circulation problems. Coiled Tubing Drilling is ideally suited to drill underbalanced and therefore a higher PIF may be achieved than might otherwise have been possible. The custom-built financial model takes into account the following factors that can be adjusted to meet operators’ requirements and current market conditions. The Oil Price With fluctuating oil prices, forecasting the price at a particular period of time is a difficult task. The model allows for either a fixed price over time or the price can be set on a monthly basis. The financial ROI model enables operators to evaluate various case scenarios, such as analysing the shortest and longest time it can take to recover the initial investment. The Total Intervention Cost The total cost must take into account all the factors involved in the intervention such as well preparation, casing, window milling and the drilling itself. Drilling underbalanced with coil is not a like for like replacement for overbalanced drilling with jointed pipe. Furthermore, the completion cost needs to be fully calculated. The Decline Curve of the Well As the well production decreases over time, so does its ability to generate cash. It is therefore important to allow for this reduction in cash flow. Different decline curves can be entered for before and after the intervention. It is obviously best to have accurate data and the decline curve for a horizontal well may be different from a vertical well. In practice though, a reasonably accurate first pass evaluation can be made with a generic decline curve and the assumption that the before and after responses are the same. Once all these assumptions and inputs are considered, the model is run. Figures 3 and 4 show graphical representations of the outputs obtained after introducing real data from an intervention. Figure 2 shows the comparison of the expected cash flow generated if an intervention had been carried out against the expected cash flow without an intervention. The point where both curves meet is the break-even point. This is when the money in the bank is the same as it would have been had the intervention not been performed. However the rate at which the money arrives at the bank is now considerably higher as shown by the gradients of the curves. This graph clearly demonstrations the potential ROI an intervention would provide for an operator. Figure 1. Revenue Projection Comparison Figure 2. Production Comparison Figure 2 highlights the increase in production when completing a well intervention. Collectively, figures 1 and 2 are compiled in a full length report, which helps operators evaluate the long term possibilities of their assets. Conclusion Underbalanced CTD is an economical solution for grassroots and re-entry drilling operations. AnTech’s financial model provides operators with the ability to evaluate an intervention before committing time and money to a project. Different scenarios can be considered with their associated effects on payback time. A complete understanding of the economics behind an intervention allows operators to get the most out of their assets. Conclusion (i) Littleton, B., Nicholson, S., and Blount, C., 2010, ‘Improved Drilling performance and economics using hybrid coiled tubing unit on the Chittim Ranch, West Texas’, IADC SPE 128926. (ii) Jahn, F., Cook, M., and Graham, M., 1998, ‘Hydrocarbon Exploration and Production - Developments in Petroleum Science Series, Vol 46 (iii) Ayan, C., Colley, N., Cowan, G., Ezekwe, E., Wannell, M., Goode, P., Halford, P., Joseph, J., Mongini, A., Obondoko,G., and Pop, J., Schlumberger, Oct 1994, ‘Measuring Permeability Anisotropy: The Latest Approach’, Oilfield Review, Vol 6, Issue 4.
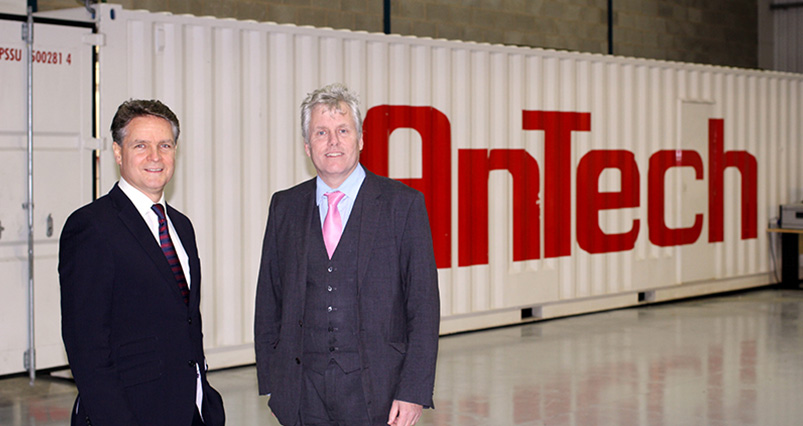
1418126400000
AnTech Further Expands Its CTD Service Division In The UK
Directional Coiled Tubing Drilling (DCTD) provider AnTech Ltd has announced the expansion of its UK premises in Exeter, UK. Due to recent and ongoing expansion, the firm has more than doubled its workshop and office footprint for its DCTD service division by over 9000 sq ft. The UK expansion follows on from a successful year of growth, including the appointment of an agent in Saudi Arabia and Bahrain and the launch of a Houston office, which has increased AnTech’s global support for its customers. Founded in 1992, AnTech operates globally across two divisions, providing DCTD services and permanent completion products supported by specialist training. Its Coiled Tubing Drilling Service division delivers cost effective directional drilling services to customers, utilising AnTech’s proprietary drilling tools, teams and systems, whilst the Products division is heavily focused on meeting the highest industry standards in the completions market. Toni Miszewski, AnTech managing director said: “We are delighted to be expanding our facilities so substantially. This enables us to focus on developing our product, particularly our service offering, which supports clients by increasing production from depleted wells using DCTD technology. As we continue to expand globally in key regions, it is vital to also continue our strategic growth plans in the UK. “AnTech has been focusing on growth within the Americas and Middle East, as well as Europe. Our team has doubled in the last year and demand for our range of patented products, wellhead equipment and state-of-the-art DCTD equipment continues to increase.” Stratton Creber Commercial Property Consultants acted for the landlords of the units which AnTech has acquired. Company director, Andrew Hosking, said: “Securing an international company as a tenant is a testament to the quality of the commercial space on offer and underpins our position as the leading provider of practical and innovative solutions in the commercial property sector. “We are particularly pleased to have assisted AnTech in its expansion to these high quality, modern workshop and office premises, which will act as a base for further local and international growth.” AnTech currently employs a team of 50, and this number is expected to grow in the coming months, across all divisions, including operations, sales, engineering and production.
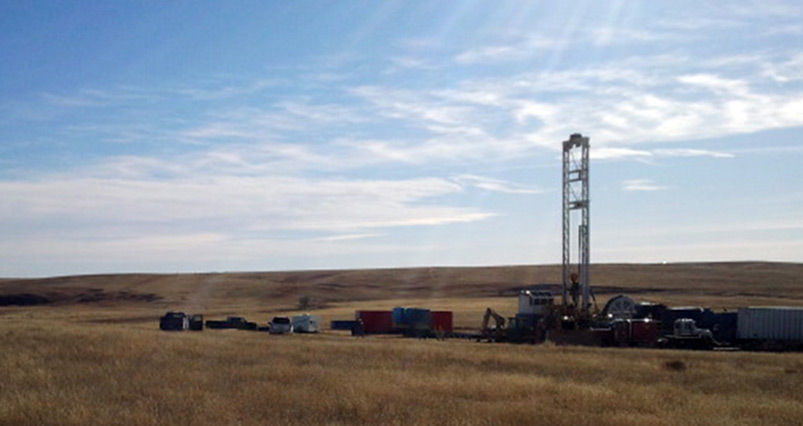
1415361600000
Directional CTD Advances Enable Drilling Of Low Margin Wells
Operators are always looking for an economical and environmentally sensitive way to access mature oil fields. It is a continuing source of frustration for the industry, because the two proven techniques for increasing reserve recovery; horizontal drilling and underbalanced drilling, are not economically combined with standard, jointed pipe drilling. Plus, the speed advantages of Coiled Tubing Drilling (CTD) cannot be fully exploited, because it doesn't lend itself to drilling directionally with larger hole sizes. AnTech Ltd, a directional coiled tubing drilling (DCTD) specialist, recognized that an economical solution lay in the speed and underbalanced capabilities of DCTD. In 2009 AnTech began developing a DCTD tool that would drill larger diameter horizontal wells. The POLARIS tool is a 5-inch OD bottom hole assembly (BHA) targeted at drilling directional, S-curve and horizontal wells. It is capable of drilling in these profiles because it is steered using AnTech’s patented solid state Acrobat gyro-directional sensor that provides horizontal gyro-while-drilling (GWD) capability. With the gyro sensor located just behind the motor, quick directional feedback is produced, providing a more precise and controlled trajectory. The POLARIS tool was developed to provide a method of using CT to drill the larger hole sizes. The introduction of the solid state gyro allowed the sensor to be located closer to the bit, almost halving the length of the BHA, which is less than 40 ft overall between bit and coil connector. It also meant that the tool could be built from less expensive standard materials without the need for non-magnetic collars and without sacrificing its GWD capability. Niobrara Drilling Campaign A five-well drilling campaign carried out by AnTech with the POLARIS tool in the Kansas Niobrara Formation demonstrated that the system reliably drills directional, S-curve and horizontal wells. AnTech designed the Niobrara campaign to put the POLARIS tool to the test, making certain that the challenging operation would demonstrate the tool’s ability to re-enter mature wells and economically access this shallow reservoir. To keep costs to a minimum, the surface of every well was drilled and casing set using a water well rig. Given the extremely low margins associated with the wells, no pad or access road was prepared in advance, further highlighting the environmental advantages of this particular program. During Phase 1, AnTech drilled three wells overbalanced with mud. The first well was an S-curve, while the remaining two wells were deviated to varying degrees. Throughout the drilling campaign AnTech used a hybrid drilling rig in cooperation with a CTD rig specialist. The benefit of using this type of drilling rig is that drilling time can be reduced by as much as 60%, as compared with drilling with conventional jointed pipe rig. Well 1 was an S-curve drilled to nearly 3000-ft. TVD and over 600-ft. lateral displacement.The reservoir targeted for drilling was situated beneath productive farmland. AnTech located the rig on neighbouring land, making certain to set the trajectory so that the landowner would not be disturbed.The reservoir targets of Wells 2 and 3 were situated below creeks, making it impossible to place the rig directly above the target, as a consequence deviated wellbores were drilled. In less than one day, the POLARIS tool accurately drilled Well 2 to more than 1500-ft. TVD with an average dog leg severity of approximately 7.5°. The third well was drilled near Goodland, Kansas, with over 1100-ft. TVD and 700-ft. lateral displacement. This third and final well of Phase 1 was completed as planned. All three wells drilled validated that the solid-state Acrobat gyro system reliably monitors the orientation of the tool, making it easy to accurately drill along a specific path. No Countryside Disruption By using the POLARIS tool to drill directionally, AnTech accessed targets without disrupting the surrounding environment. This could not have been achieved had the wells had been drilled vertically. Located under a hill, riverbed, and bordering a cornfield, they were situated in areas without drill pads in place or access roads. The only way low margin operations such as these make economic sense is to make certain that they are mobilized and drilled rapidly. Phase 1 confirms that this is achievable. Due to the highly fractured formation that was incapable of supporting the pressure of a liquid column, air was used to drill Wells 4 and 5 in Phase 2. Using an 8-1/2-inch bit, the build sections of these wells were drilled with mud, while the horizontal sections were drilled with an air mist using a 6-1/4-inch bit. A unique benefit of the POLARIS tool is that it produces reports of downhole vibration in real time. In Phase 2, the accelerometers recorded shock spikes of up to 350g during air drilling; more specifically with the bit off-bottom. Measurements of vibration are extremely important during operations such as this, so it is critical that the equipment can withstand the punishing vibration and shock experiences when drilling with aerated fluids or in air. Well 4 was drilled horizontally to 1090-ft. TVD and over 1450-ft. lateral displacement. AnTech then executed the final operation on horizontal Well 5, drilling it to 1096-ft. TVD with a lateral displacement of 1103-ft.The final two wells drilled highlighted the effectiveness of the POLARIS tool, which successfully drilled horizontal and directional wells. Field Performance Phase 1 benefited from the POLARIS tool’s ability to target a precise location within the reservoir without having to position the rig directly above the target. During Phase 2, directional CTD was used to air-drill a reservoir that was incapable of supporting a liquid column. This is an ideal example of an application where CTD has an advantage. Overall, the program illustrated that by using the POLARIS tool, it is possible to drill horizontal and directional wells with 6.25-in. to 8.5-in. holes, while using mud and an air mist as a drilling fluid. For AnTech, it was particularly significant because it was the first time that a solid state gyro had been used for directional measurement while drilling. The Acrobat gyro system generated valuable data at all inclinations, including horizontal, which meant that orientation was accurate, even in the casing. The program offers firm evidence that wells can be drilled in shallow reserves without affecting the environment or requiring heavy investment. Furthermore, it illustrates that well plans can be followed precisely. Well paths can also be enhanced by kicking off early with the gyro situated in the casing, which reduces build rates, making casing running more efficient. In addition to the POLARIS tool and the experienced CTD team, AnTech attributes its success to the hybrid drilling rig. Without the hybrid drilling rig – which runs CT and jointed pipe as well as running and pulling casing – these operations would not have been possible. Because they are so adaptable, CTD is easily achieved with a single rig, efficiently and economically. DCTD Suitability For years, CTD has been the method of choice for drilling underbalanced within a reservoir. Now that CTD can directionally drill much larger holes, fields previously thought to be inaccessible because they didn’t make economic sense to access, can be exploited, making low margin drilling operations a viable proposition. Operators should consider CTD for re-entry and development programs where the reservoir and geology conditions are uncomplicated. For those planning to carry out a standalone or wildcat project, CTD is not the answer because the benefits of efficiency and speed do not have the chance to be fully realized. In addition to the applications illustrated by the Niobrara program, DCTD is highly beneficial when drilling in these circumstances: Multilateral branches from the main wellbore. -Several wells from a single pad, where it is key to use the gyro orienting capability to avoid intersecting with other wells.In areas where a minimal environmental footprint is critical: commercial, residential or farming regions.In sensitive reservoirs that would experience excessive skin damage caused by overbalanced drilling. During the past 20 years, CTD has been embraced as a means of accessing untapped reservoirs, particularly in Alaska, Russia and Saudi Arabia for directional wells and Canada and the Lower 48 for vertical wells. Currently, there are CTD operations being undertaken in Malaysia and Australia. Given the cost-savings, speed, and environmental benefits it provides, DCTD is gathering wider market acceptance. With the arrival of new technologies, such as the POLARIS tool that drills simple shallow wells to multiple wells from a single pad, directional CTD’s time has come.
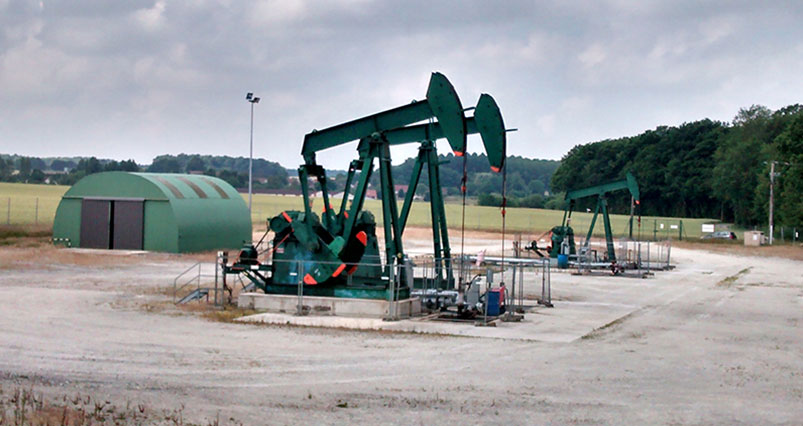
1407758400000
Lundin Petroleum Award Underbalanced Coiled Tubing Drilling Contract To AnTech
UK firm AnTech Ltd has been appointed by Lundin Petroleum (Lundin) to carry out an Underbalanced Coiled Tubing Drilling (CTUBD) project to ensure maximum oil recovery from its assets in Europe. The program builds on a similar, successful project which was completed in 2007. CTUBD allows the wells to be extended without damaging the existing wellbore. This is something that is only possible with this technique. AnTech’s POLARIS Bottom Hole Assembly (BHA) has been purpose built for this type of application, allowing new horizontal drainage holes to be used to offer enhanced oil recovery in a safe, environmentally responsible and efficient way. Toni Miszewski, Managing Director, AnTech said “This is an exciting project for the AnTech team, and Lundin will be able to take advantage of 22 years of providing specialist solutions to the oil and gas sector. As operating companies seek to produce more from existing wells, Coiled Tubing Drilling is increasingly seen as a cost-effective way for them to do that. “We are delighted to have been appointed by Lundin Petroleum and believe our offerings sit well with the organisations’ values of ensuring maximum oil recovery in a safe and environmentally responsible way.” The project is based in Lundin Petroleum’s operational Villerperdue oilfield in France, within the Paris basin. The fields continue to provide opportunities for non-drained wells to be accessed and recovered. Fabrice Crouzet, Drilling Manager, Lundin said “We have selected AnTech for their technical capability that they can bring to this project with their 5” POLARIS BHA. This is the first time a BHA of this size will be deployed in Europe so we are looking forward to working with them on this campaign and enhancing our production". Lundin Petroleum is a Swedish independent oil and gas exploration and production company with a well balanced portfolio of worldclass assets primarily located in Europe and South East Asia.
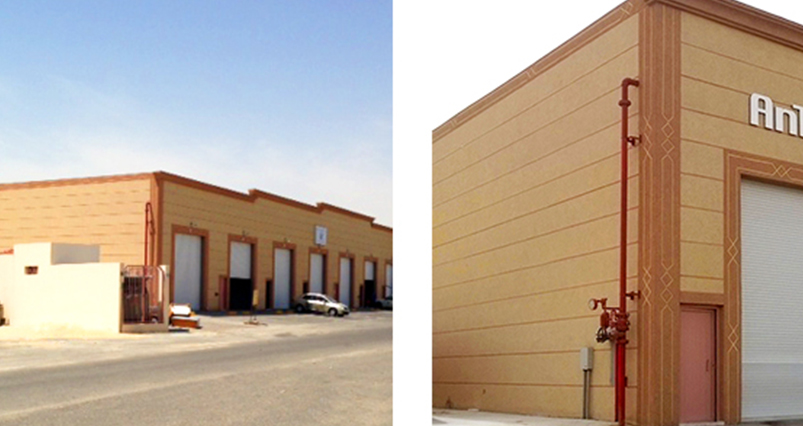
1402660800000
AnTech Expands In The Middle East And Opened A New Office
Directional Coiled Tubing Drilling (DCTD) provider AnTech Ltd has announced it has appointed a Saudi agent and opened a new office in Al-Khobar, Saudi Arabia. Having secured significant investment from Saudi Aramco Energy Ventures and Calculus Capital last year, the UK firm has appointed The Al-Shuwayer Group as an agent for Saudi and Bahrain. This follows on from AnTech’s expansion in the US, with the launch of its Houston office last year, to build on the firm’s global growth strategy. Founded in 1992, AnTech operates across three divisions, providing innovative product technologies, DCTD services and specialist training for the global upstream oil and gas industry. Its Coiled Tubing Drilling Service division delivers cost-effective directional drilling services to customers utilising AnTech’s proprietary drilling tools, teams and systems, whilst the Products division is heavily focussed on design innovation and custom solutions to meet clients’ individual needs. The training is delivered through the AnTech Academy, which provides specialist training in Coiled Tubing Drilling as well as training for its own range of products for the industry. AnTech plans to reveal roll out plans for its Academy in the near future. Toni Miszewski, Managing Director, AnTech said “It is an exciting time of growth for AnTech and we are pleased to announce our partnership with The Al-Shuwayer Group. It is increasingly important that we are able to offer the best possible service to our clients in the Middle East, hence our strategic expansion within the region. AnTech has been focussing on growth within the Americas and Middle East, as well as Europe. Its staff numbers have doubled in the last year and demand for its patented products, wellhead equipment and state-of-the-art DCTD equipment continues to increase in new regions.“ Toni added: “Anas Al-Shuwayer, Managing Director of The Al-Shuwayer Group has over 18 years of oilfield experience and has been crucial in advancing new projects for leading companies in the oil and gas industry. Combined with AnTech’s in-house R&D team, our new Al-Khobar base will provide specialist DCTD Services which can bring significant benefits to operators in The Kingdom.” AnTech offers its COLT Bottom Hole Assembly (BHA) for smaller diameter thru-tubing drilling and its gyro-steered POLARIS BHA for larger side-tracks and grass root wells. Both have been successfully deployed in field operations for wells in underbalanced conditions, using aerated fluids. In fact, the POLARIS BHA was used for drilling the world’s first horizontal lateral with air. AnTech will continue to develop its drilling tool portfolio in the future to further service its global customer demand.
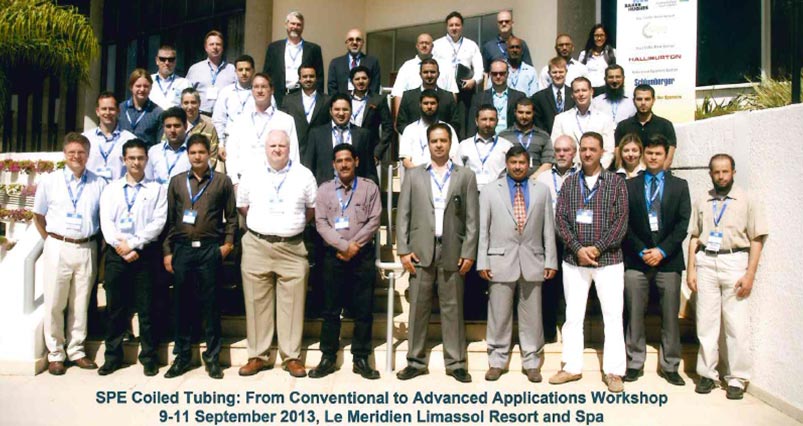
1378900800000
AnTech's MD Presents At Coiled Tubing Workshop
AnTech's Managing Director, Toni Miszewski travelled to Limassol in Cyprus this September for Society of Petroleum Engineers (SPE) Conference, where he presented at the Coiled Tubing Drilling: From Conventional to Advanced Applications Workshop. Workshop attendees discussed Coiled Tubing (CT) intervention experiences, best practices, and case studies from operating companies, CT service providers, CT pipe manufacturers, CT surface and down hole equipment and tools manufacturers, and wellhead and completion companies. To find out more about the workshop or SPE, please visit: SPE
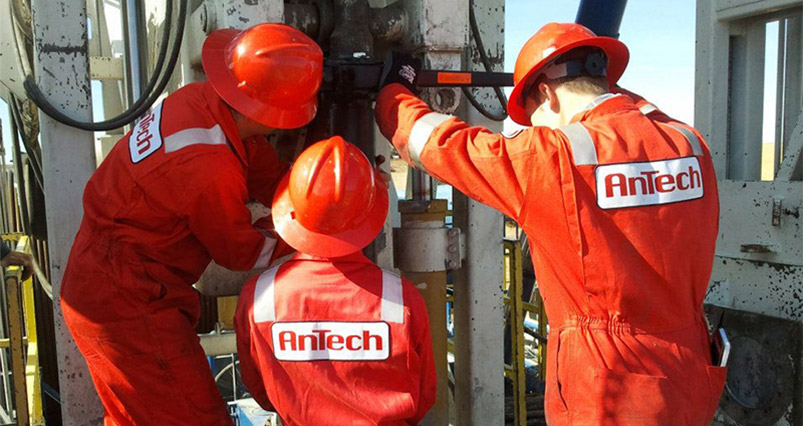
1373025600000
Saudi Aramco Energy Ventures & Calculus Invest
AnTech has received funding from investors to launch its new Directional Coiled Tubing Drilling (CTD) Service capability. AnTech has its sights firmly set on providing Directional CTD Services with its field-proven drilling systems for operators seeking to access reserves in the unconventional, shale and re-entry markets, focussing initially in the United States, Europe and the Middle East. Already, the results of the recent cash installments are taking shape as the company gears up to provide drilling campaigns to customers. During recent months, AnTech has doubled the size of its engineering team, and is actively recruiting for additional experienced CTD engineers and support staff. It has also expanded its global headquarters in Exeter, England to provide improved operations, manufacturing and maintenance facilities. To support operations in North America, the company’s new base in Houston will open its doors soon, with an operations manager already appointed. The news was also featured on BBC Spotlight (UK-South West News) and is shown below:
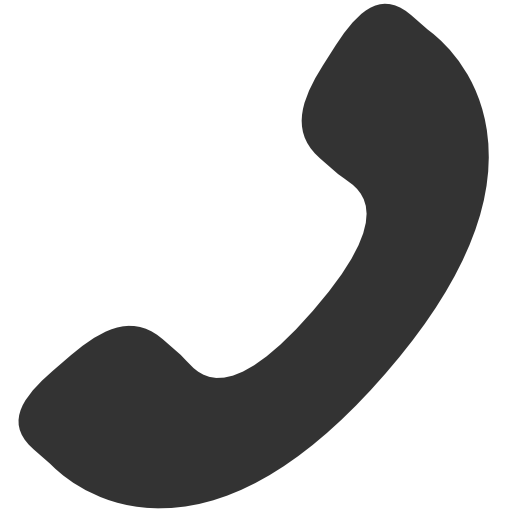
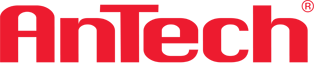
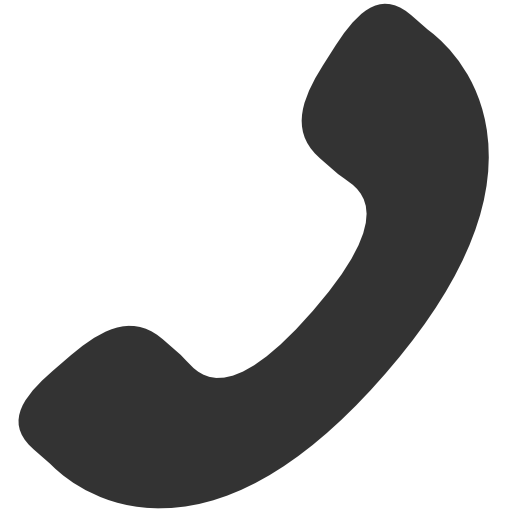

+44 1392 933 100 | +1 800-868-1562